申請人:清華大學
發(fā)明人:馮雪 蔡世生 張長興 李海成 張迎超 韓志遠
摘要: 本發(fā)明公布了一種基于納米金剛石顆粒的大規(guī)模芯片純機械無化學式減薄方法,屬于柔性可延展光子/電子器件、半導體以及微電子技術(shù)領(lǐng)域。本發(fā)明方法利用納米金剛石顆粒作為磨削材料純機械無化學式減薄各種芯片材料(電子、光子芯片等);在減薄過程中,通過改變納米金剛石的粒徑來調(diào)控粗糙、中度、精細研磨以及拋光;通過調(diào)控芯片托盤的芯片槽的大小來實現(xiàn)不同尺寸芯片的大規(guī)模減薄。本發(fā)明方法適用于各種芯片材料大規(guī)模的減薄,同時適用于減薄到任意厚度,最終厚度可達到10μm左右,能夠很好地契合柔性可延展光子/電子器件所需的器件厚度。
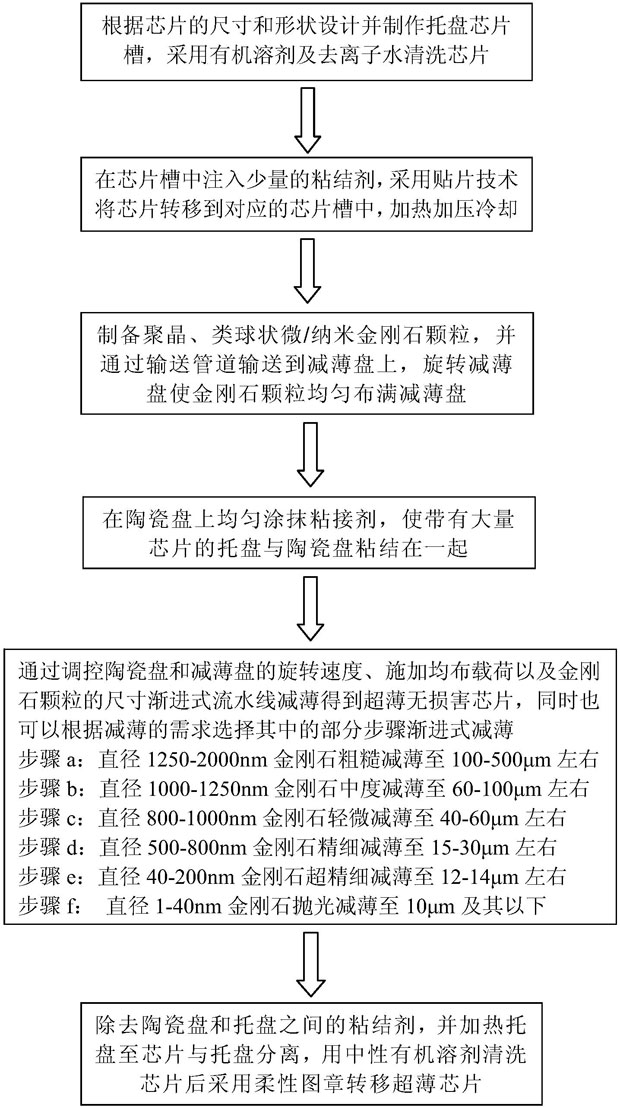
2.如權(quán)利要求1所述的方法,其特征在于,在步驟4)利用粒徑分布在2000nm至1nm范圍內(nèi)的多種不同粒徑的金剛石顆粒,按顆粒粒徑從大到小的順序依次對芯片進行減薄,最后減薄采用的金剛石顆粒的粒徑為40-200nm和/或1-40nm。
3.如權(quán)利要求1所述的方法,其特征在于,在步驟4)選擇如下a至f中的兩個或更多個步驟按金剛石顆粒粒徑從大到小的順序進行漸進式芯片減?。篴:將陶瓷盤安放在一號減薄盤上并施加均布載荷,一號減薄盤上的金剛石顆粒的粒徑在1250-2000nm,減薄芯片厚度至一定厚度;b:將陶瓷盤移動至二號減薄盤上并施加均布載荷,二號減薄盤上的金剛石顆粒的粒徑為1000-1250nm,減薄芯片厚度至一定厚度;c:將陶瓷盤移動至三號減薄盤上并施加均布載荷,三號減薄盤上的金剛石顆粒的粒徑為800-1000nm,減薄芯片厚度至一定厚度;d:將陶瓷盤移動至四號減薄盤上并施加均布載荷,四號減薄盤上的金剛石顆粒的粒徑為500-800nm,減薄芯片厚度至一定厚度;e:將陶瓷盤移動至五號減薄盤上并施加均布載荷,五號減薄盤上的金剛石顆粒的粒徑為40-200nm,減薄芯片厚度至一定厚度;f:將陶瓷盤移動至六號減薄盤上并施加均布載荷,六號減薄盤上的金剛石顆粒的粒徑為1-40nm,減薄芯片厚度至一定厚度。
4.如權(quán)利要求1所述的方法,其特征在于,在步驟4)中,當使用的金剛石顆粒粒徑在1000-2000nm時,采用4-7.5莫氏硬度的減薄盤;當使用的金剛石顆粒粒徑在500-1000nm時,采用2-4莫氏硬度的減薄盤;當使用的金剛石顆粒粒徑在500nm以下時,采用1-2莫氏硬度的減薄盤。
5.如權(quán)利要求1所述的方法,其特征在于,步驟4)進行減薄操作時,在陶瓷盤上施加每個芯片承受的載荷為0.5-1.5KPa的均布載荷,陶瓷盤和減薄盤的旋轉(zhuǎn)速度分別為30-80rpm和30-40rpm。
6.如權(quán)利要求1所述的方法,其特征在于,在步驟4)的減薄過程中通過管道輸送金剛石顆粒到減薄盤上進行補給。
7.如權(quán)利要求1所述的方法,其特征在于,步驟1)中采用有機溶劑和去離子水依次清洗待減薄的芯片,然后在芯片槽中注入少量的粘結(jié)劑,采用貼片技術(shù)將各尺寸及形狀的芯片放置于對應的芯片槽中,加熱芯片托盤,并加壓后冷卻,使芯片貼合到芯片槽中。
8.如權(quán)利要求1所述的方法,其特征在于,步驟2)在陶瓷盤上均勻涂覆粘結(jié)劑,將芯片托盤底面黏附于陶瓷盤上。
9.如權(quán)利要求1所述的方法,其特征在于,步驟4)通過輸送管道輸送金剛石顆粒到減薄盤上,通過旋轉(zhuǎn)機器驅(qū)動減薄盤旋轉(zhuǎn)并控制旋轉(zhuǎn)速度,在整個減薄過程中,采用修正環(huán)促使金剛石顆粒均勻地布滿整個減薄盤。
10.如權(quán)利要求1所述的方法,其特征在于,步驟5)用中性有機溶劑清洗芯片時,芯片會依托在芯片托盤的芯片槽中,使用柔性圖章選擇性轉(zhuǎn)移不同功能的芯片至特定基底上。