航空發(fā)動機、燃氣輪機葉輪(整體葉盤)、葉片加工難點與其葉型形狀結構及加工質量要求特點直接相關,葉型在整體上具有的不規(guī)則三維空間曲面形式,使得其加工方式上構成了專業(yè)性質,而其同時具有的薄壁形式,又成為曲面結構精度要求達到始終不能避免的影響因素,葉型表面質量近乎苛刻的要求,也是成型精度保證在加工方式選擇上必須考慮的問題。
由于葉輪(整體葉盤)、葉片的葉型是對航空發(fā)動機、燃氣輪機中的高溫高壓的氣體介質實施作用,受到離心、氣體沖刷與復合振動等性質的交變應力作用,使得其材料性質必須具有輕質、高強度、高耐疲勞性能及耐腐蝕等綜合性能,為此,零件材料就呈現(xiàn)了復雜的難加工性質,從而加劇了其加工的更大難度。為了實現(xiàn)葉輪(整體葉盤)、葉片高質量與高效的加工需求,其加工技術具有多專業(yè)、多種形式及持續(xù)性的創(chuàng)新發(fā)展,以適應產品結構與材料改變所富裕功能不斷提高所具有的需求。
多軸聯(lián)動加工中心設備對葉片制造技術發(fā)展的促進
1. 葉片型面凈成型制造技術的發(fā)展
葉片制造傳統(tǒng)的高效加工技術發(fā)展,主要是體現(xiàn)在葉型的凈成型方面,即降低或完全去除葉型機械加工切削量(其中包含很多的手工鉗修打磨操作)的方式來實現(xiàn)加工效率的提升,其中具有代表性的技術是精鍛、輥軋與精鑄技術(見圖1)。
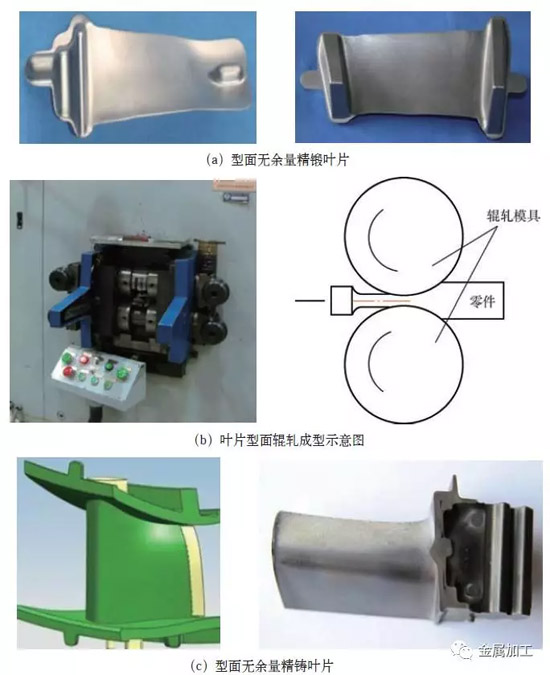
目前,隨著電加工、機械加工等的多軸聯(lián)動數(shù)控加工技術發(fā)展,以及機械手等先進加工技術的日新月異,使得模具加工精度水平實現(xiàn)與熱加工相關流程中影響因素獲得了較好控制,從而使葉片葉型的凈成型加工獲得很好的提高發(fā)展;并且由于多軸聯(lián)動數(shù)控銑削、磨削加工的發(fā)展,使得利用精鍛與輥軋形成葉型的進排氣邊補充加工,也由原來的手工打磨方式改變?yōu)闄C械控制加工方式,加工質量與效率水平也得到了促進提高,使傳統(tǒng)的高效加工技術獲得了新的促進發(fā)展。
2. 葉片加工快速反應能力提升技術發(fā)展
由于多軸聯(lián)動數(shù)控切磨削加工技術的發(fā)展,使得葉片制造適應新機研制需求的快速反應能力獲得了非常大的提升。傳統(tǒng)的葉片加工工藝,因為葉片結構上的不規(guī)則形狀,加工數(shù)量的成批性質,以及設備功能的局限性,使得葉片的緣板、榫頭及型面等部位必須單獨進行加工,加工工藝呈現(xiàn)很大的分散性,專用工裝多,工序長,周轉多,效率低。該種加工方式對于新機研制而言所存在的弊端尤其難以令人接受,主要體現(xiàn)是生產準備時間長,工序加工調試時間占比大,周轉與加工時間比例不協(xié)調,完全不能滿足新機研制所需的快速反應要求。
隨著功能強大的多軸聯(lián)動數(shù)控加工中心設備的出現(xiàn),葉片加工工藝的改變具有了非常良好的基礎。目前新機葉片研制的高效加工方式是,通過葉片兩端工藝凸臺的施加,使葉片能夠實現(xiàn)一次裝夾完成緣板、榫頭和型面幾乎全部位置的集成化加工,其專用工裝數(shù)量減少可達90%,加工周轉占比時間縮短可達80%,極大地提高了研制的快速反應能力。比較典型的兩種集成化加工工藝方式如圖2、圖3所示。
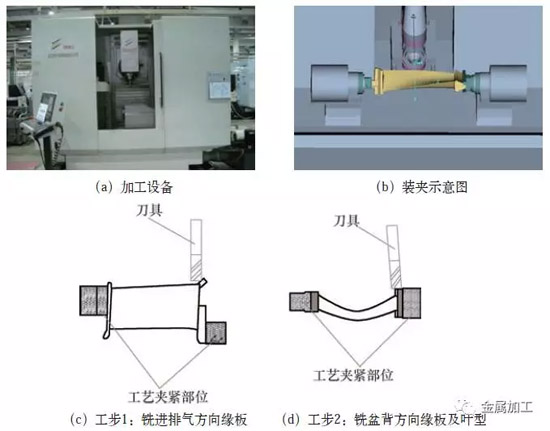

發(fā)動機整體葉盤結構(見圖4)的出現(xiàn),很大層面的因素是由于多軸聯(lián)動數(shù)控加工設備與編程軟件控制技術的發(fā)展,盡管整體葉盤的粗加工開槽方式先后出現(xiàn)了水切割、電火花銑削等方式(見圖5),但是由于整體葉盤、葉片之間流道所呈現(xiàn)的非線性且狹窄空間的特點,使得葉片型面幾何精度的最終保證,仍然主要依靠于多軸聯(lián)動數(shù)控加工中心設備的功能作用。
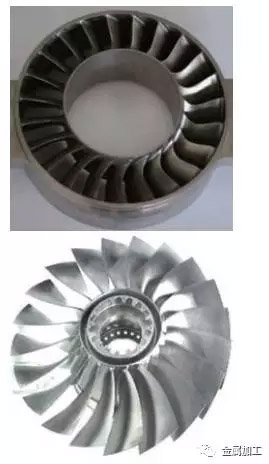
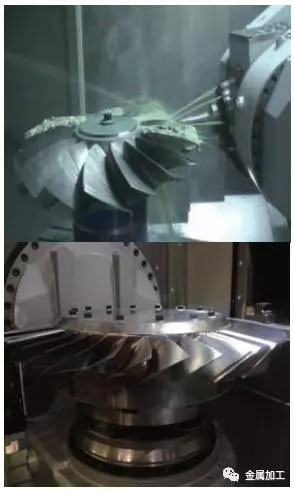
1. 葉片型面精密振動電解
加工技術發(fā)展葉片型面的多軸聯(lián)動加工方式盡管能夠實現(xiàn)較好的快速反應能力,但其刀具的加工成本是非常大的,尤其對于高溫合金一類的難加工材料而言,刀具損耗量幾乎可以占到成本的30%~40%,并且型面的成型加工是走刀軌跡的集成,加工效率的提升空間有很大的局限性。
而葉片型面精鍛、輥軋的凈成型加工技術,存在著加工變形、加工精度保證難度大的問題,并且該兩種方式還存在進排氣邊圓弧部分需要補加工的問題,補加工部分與已有型面部分的交接完好程度保證難度也比較大。
目前,新型的振動電解加工設備的出現(xiàn),改變了型面加工精度保證、成本降低與效率提升之間的矛盾,其加工精度可達到0.02mm左右水平,由于加工是利用電極的全型面復映方式,葉片盆背兩側加工可以兩端同時進給加工,效率水平高,并且理論上而言電極是不磨損的,因此,成本上也較低,但是對于葉片型面精度的達到,應該是有一定難度的,需要對電解液、電解參數(shù)及電極精度等因素的匹配控制,對于大批量葉片加工具有優(yōu)勢。以多軸聯(lián)動數(shù)控加工中心設備與精密電解加工設備所形成批量生產工藝,具有加工精度質量得到可靠保證,并且具有高效率、低成本的特點,是葉片制造走向高質、高效加工的有效途徑。
2. 葉片超塑成型加工技術
發(fā)展目前先進航空發(fā)動機風扇轉子葉片普遍采用小展弦比的寬弦葉片,其主要目的是增大單級葉片的氣動效率,同時解決振動與抗外來物打傷的能力,但是如果該種葉片采用傳統(tǒng)的制造方式則存在質量大大增加的問題,發(fā)動機輪盤難以承受大質量葉片旋轉后形成的強大離心力。
為了解決相關問題,目前的做法是將葉片做成空心或使用復合材料進行制造,采用鈦合金進行制造的一種技術是,葉盆和葉背為兩個分體的板片結構,利用材料的超塑性能使用模具進行成型,在成型的同時采用新型的擴散連接焊接技術將分體結構聯(lián)結為一個整體葉片,中部空心部分采用蜂窩夾芯進行剛性加強,如圖6所示。
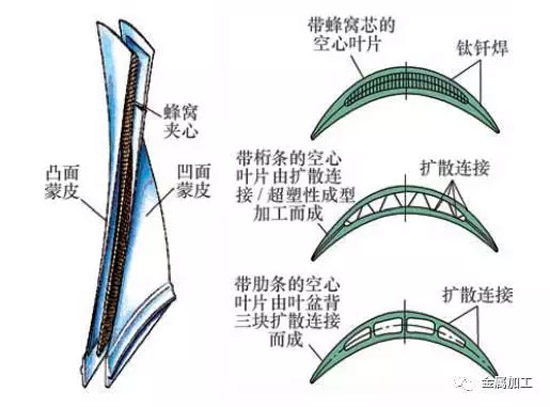
3. 雙性能整體葉盤制造技術
目前壓氣機部分的整體葉盤基本是盤體和葉片采用同種金屬材料,其制造基本是采用一個盤件的鍛件通過最終加工成形。
而渦輪部分的整體葉盤則根據盤體和葉片工作環(huán)境差異,而采用不同的材料進行制造,比較典型的是由高溫合金粉末盤與單晶高溫合金葉片復合成形為整體葉盤。在制造工藝上,高溫合金粉末盤與葉片分別采用熱等靜壓法和鑄造完成坯料制造,然后經過機加工分別完成各自成形加工,最后采用以下之一的方式完成雙性能的整體葉盤制造,分別是:電子束焊接法、擴散連接法、線性摩擦焊接法及鍛接法等,其使發(fā)動機的功能實現(xiàn)幾乎達到了極致完美狀態(tài)。
4. 葉片3D打印凈成型加工技術
3D打印對于復雜的葉片坯料制造工藝改變具有非常大的意義,利用激光熔化燒結鈦合金、高溫合金粉末材料進行的葉片坯料制造,改變了傳統(tǒng)鍛、鑄造工藝需要進行模具制造,多道次的加熱鍛打,或進行蠟型壓制、型殼制造及澆鑄等的眾多工藝環(huán)節(jié),大大簡化了制造流程,并且具有較迅速的快速制造能力。
目前3D打印技術進行的葉片坯料制造,具有型面或空心內腔表面實現(xiàn)凈成型,其他表面余量精確控制的狀態(tài)。然而,產品制造所需的粉末材料性能保證、坯料冶金缺陷質量控制、熱處理等技術滿足使用要求的程度,仍然是制約工程化應用的重點研究環(huán)節(jié)。但是隨著研究工作的不斷進行,3D打印的葉片制造技術正在不斷完善,其應用已經越來越接近于成熟。
結語
葉片與葉輪是發(fā)動機和燃氣輪機氣動性能與效率功能實現(xiàn)的直接作用部件,其非常大地決定了發(fā)動機和燃氣輪機的功能性質,多年來其材料技術、結構技術改變從來沒有停止過。
伴隨著零件材料與結構的創(chuàng)新性發(fā)展,其制造技術也呈現(xiàn)了多學科與多個領域的技術復合,其中包含著成型的實現(xiàn),也包含加工效率、成本等綜合效益方面的需求,無論哪一個方面技術的突破,都能夠推動產品專業(yè)的進步,進而極大地影響發(fā)動機和燃氣輪機整體制造技術的進步。
我們相信,只要發(fā)動機和燃氣輪機原理功能不發(fā)生變化,葉片與葉輪制造技術的發(fā)展與進步則仍然不會停止,進而繼續(xù)極大地影響發(fā)動機和燃氣輪機技術的發(fā)展與進步。