關(guān)鍵詞:砂輪,金剛石,陶瓷
1 引言
氧化鋁、碳化硅、氮化硅和氧化鋯等工程陶瓷由于其優(yōu)越的機械、化學(xué)和熱性能而廣泛應(yīng)用于精密工程組件的制造。磨削作為工程陶瓷組件制備工藝的最后關(guān)鍵的一步,主要完成表面粗糙度和幾何精度加工處理。而在磨削過程中,嚴重的磨粒脫落和磨損會導(dǎo)致砂輪表面的廓形誤差并引起磨削表面幾何形狀的誤差。
電鍍金剛石砂輪由于加工效率高、靈活性強而應(yīng)用于工程陶瓷材料的磨削加工。為保證表面粗糙度和外形精度,電鍍砂輪的設(shè)計必須保證有足夠的磨粒突出和微結(jié)合力,如圖一(a)所示。目前,設(shè)計出一個較好的砂輪仍然處于探索階段。難點在于結(jié)合成厚度的優(yōu)化。為了將微粘結(jié)力最大化,電鍍層厚度需要縮小,如圖一(c)所示;并由此也導(dǎo)致磨粒突出程度降低,切屑清理空間變小,如圖一(b)所示。因此,粘結(jié)層厚度度必須控制在一個適當?shù)姆秶鷥?nèi),以保證磨粒突出程度和足夠的粘結(jié)力。
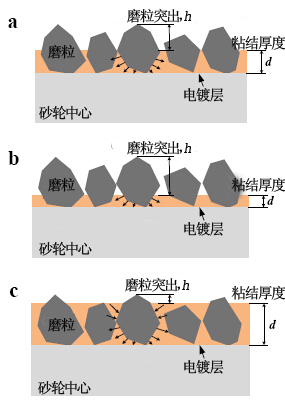
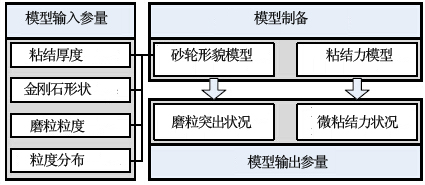
粘結(jié)層厚度和磨粒突出狀況的相關(guān)性可以由實驗測量和實際砂輪模型求得。本研究根據(jù)參考文獻中已有的實際砂輪模型對磨粒突出狀況進行分析。砂輪建模的方法是利用數(shù)學(xué)模型來復(fù)制每個砂輪的制備步驟,包括磨粒生產(chǎn)、磨粒植入和電鍍,如圖三所示。建模既考慮了砂輪組份,如磨粒粒度、粒徑分布、磨粒形狀和電鍍層厚度,還考慮了砂輪表面磨粒緊密堆積的機械學(xué)。圖四描述了單層金剛石表面形貌模擬的緊密堆積算法。首先,在粒徑分布范圍內(nèi)任意位置上生產(chǎn)出一顆六邊形的金剛石磨粒,如圖4(a);然后,該磨粒開始向下移動至已存在的磨粒并和其中一個六邊形磨粒接觸并沿著接觸點旋轉(zhuǎn),如圖4(b);最后,當該磨粒和另外的磨粒接觸并形成穩(wěn)定的支撐結(jié)構(gòu)后,磨粒旋轉(zhuǎn)停止,如圖4(c)。當磨粒堆積沒有空間時,該步驟停止,在砂輪中心形成最終的致密堆積。

圖四:(a)初始隨機位置上制備一顆六邊形的磨粒;(b)該磨粒向下移動并和另外一顆六邊形磨粒接觸;(c)磨粒旋轉(zhuǎn)并和另外一顆磨粒接觸并形成穩(wěn)定結(jié)構(gòu)
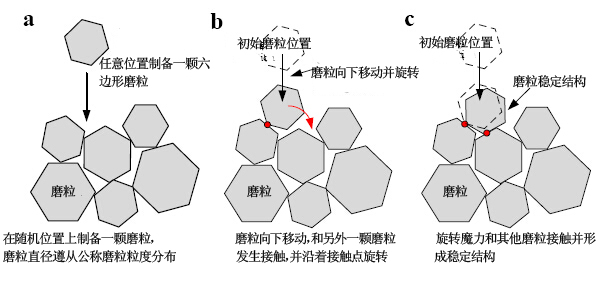
圖五:(a)金剛石磨粒(b)測量的砂輪(c)建模砂輪
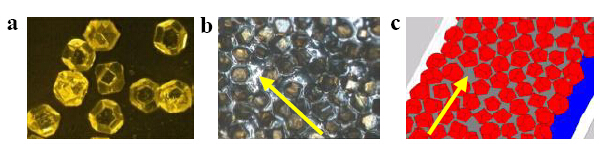
除了直接的肉眼可觀察的對比外,模擬結(jié)果和實驗測量結(jié)果在磨粒突出高度值上也進行了對比。對磨粒大小為341.2μm、213.8μm和138.2μm的金剛石砂輪的磨粒突出狀況進行測量和模擬。利用Keyence VK-X100白光顯微鏡對砂輪表面進行測量。如圖六(a)所示,從測量粒度的峰值中提取橫截面。橫截面輪廓的峰值和谷值之間的差別和磨粒突出的高度相關(guān),如圖六(b)所示。圖7為磨粒突出高度分布對比圖,可以看出模擬和實驗測量得到的磨粒突出平均值和分布范圍之間的誤差接近50%左右。
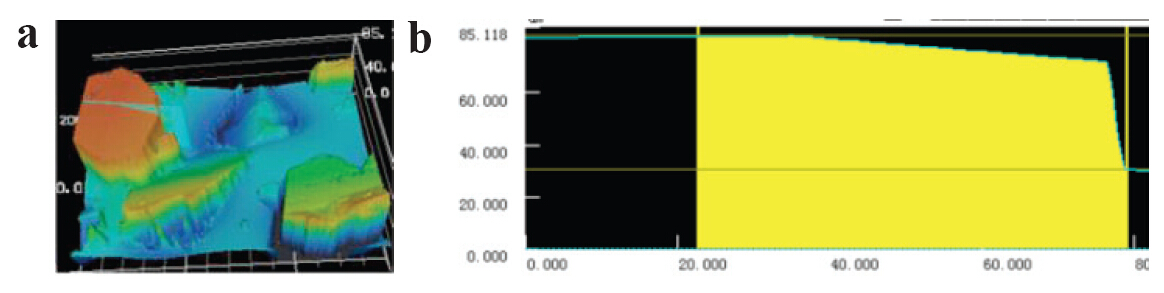
圖七:實驗測量和模擬中的磨粒突出高度對比
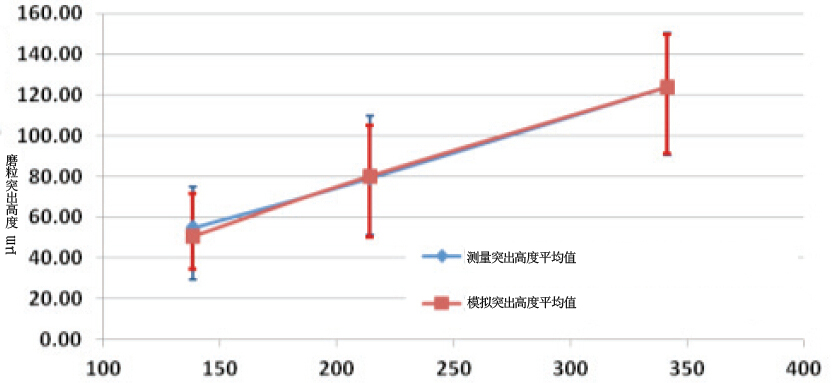
圖九:(a)金剛石磨粒;(b)磨粒夾持;(c)單顆磨粒嵌入
圖十:(a)實驗結(jié)構(gòu)圖;(b)工具移動過程中的力信號
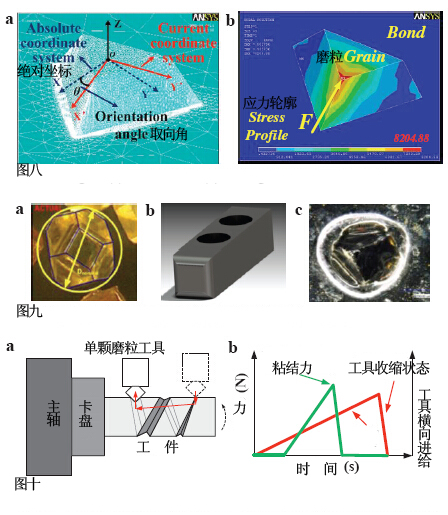
為保證切割進程中的精度,實驗使用2μm高精度數(shù)控機床,如圖11(a)所示。單顆磨粒切割工具固定在測力計頂部(測力計精度0.01N)。模擬和實驗中的磨粒脫落對比如圖12所示??梢钥闯瞿チ:驼辰Y(jié)劑界面角落處由于粘結(jié)材料的無效而導(dǎo)致磨粒脫落。

4 無磨粒脫落砂輪的制備
為制備工程陶瓷材料磨削工藝用無磨粒脫落砂輪,粘結(jié)層厚度的設(shè)計必須滿足以下條件:1)所有磨粒最小粘結(jié)力必須大于最大微切割力(見公式1);2)所有磨粒突出高度必須大于0(見公式2);任意磨粒的微切割力在0N-5N之間變化。
Fb(Gi)>Fc(Gi) (1)
h(Gi)>0 (2)
本論文中,砂輪所用磨粒材料為#375金剛石磨粒,3.6μm標準誤差。磨粒形狀為六邊形,有6個方形面和12個六邊形面構(gòu)成。為驗證粘結(jié)厚度的最佳范圍值,分別利用17、24、31、38μm厚度進行實驗。粘結(jié)層材料為原子比為3:1的Ni-Co合金。表二為砂輪形貌模型和粘結(jié)力模型的模擬參數(shù)。
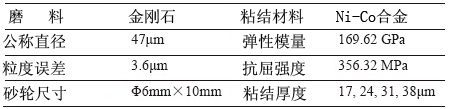
圖14:最大粘結(jié)厚度計算
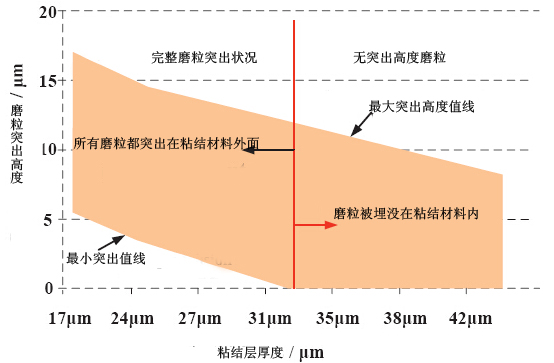
在粘結(jié)層厚度值周期內(nèi),為合成微粘結(jié)力范圍,研究利用反應(yīng)曲面分類研究法(RSM)研究多輸入變量對性能指標和質(zhì)量特性的潛在影響。因此,預(yù)期輸出指標可以表達為輸入工藝參數(shù)(晶粒取向、粘結(jié)層厚度)的一個多項式函數(shù),如公式3所示。由工藝參數(shù)組成的函數(shù)叫做響應(yīng)面。對于所有預(yù)測變量,通常利用二階模型求得多項式近似值,如公式4所示。在所有預(yù)測變量中,OA和TOB為磨粒取向角度和粘結(jié)層厚度。Fbonding為對應(yīng)條件的粘結(jié)力。對于模型回歸程序,研究利用最小二乘法,如公式5所示。
Fbonding=f(x1,x2)=f(OA,TOB) (3)
y=bo+ (4)
S(θ)= (5)
其中,OA為取向角度,TOB為粘結(jié)層厚度。
考慮到磨粒的對稱特性,分別選擇0°、16°、30°、45°和60°的取向角。粘結(jié)層厚度選擇17μm、24μm、31μm和38μm,涵蓋了磨粒直徑的36.2%到80.9%。表三為所有條件下的模擬結(jié)果?;貧w模型如公式6所示。對于每一個粘結(jié)厚度值,可以根據(jù)回歸公式計算最大粘結(jié)力和最小粘結(jié)力。對最大、最小粘結(jié)力進行排列,可以求得粘結(jié)層厚度值范圍內(nèi)的微粘結(jié)力周期。
通過將5N設(shè)置為最小粘結(jié)力的臨界值可以推斷出最小粘結(jié)層厚度必須大于24μm才能夠降低磨削工藝中磨粒脫落的可能性,如圖15所示。
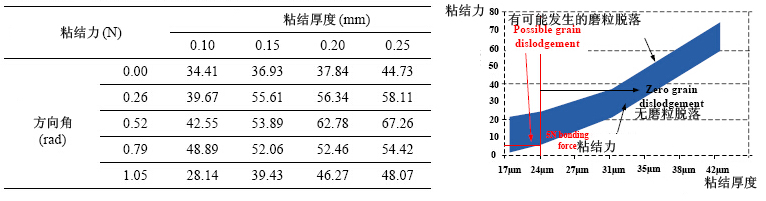
對磨粒突出情況的研究以及微粘結(jié)力變量作為粘結(jié)層厚度值的一個函數(shù)有助于電鍍金剛石砂輪的優(yōu)化設(shè)計參數(shù)。為保證100%的磨粒突出,粘結(jié)厚度不能大于33μm;為克服磨削工藝中的微切削力,粘結(jié)厚度值不低于24μm。圖16中,將兩個范圍值疊加可以求得粘結(jié)層厚度值的最佳范圍值,在24μm~33μm之間。
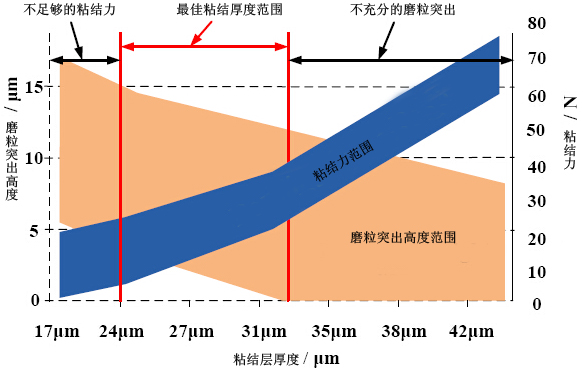
為驗證砂輪最佳設(shè)計方法的有效性,實驗制備了三種粘結(jié)層厚度不同的砂輪用于磨削試驗,參數(shù)如表四所示。根據(jù)上述研究,37μm粘結(jié)層厚度的砂輪C的磨粒突出程度不能達到100%;21μm粘結(jié)層厚度的砂輪A不能有足夠的微粘結(jié)力;30μm粘結(jié)層厚度的砂輪B在磨粒突出和無磨粒脫落方面要稍有缺陷。

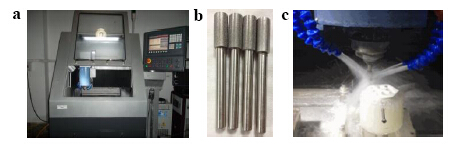
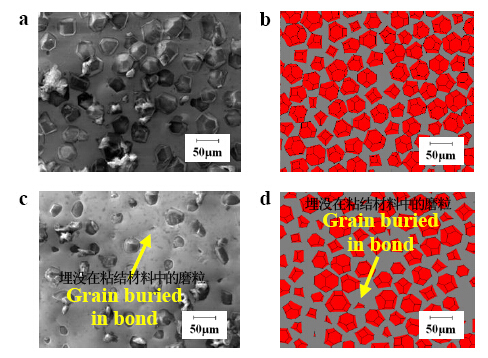
本研究建立了一種制備電鍍砂輪的數(shù)字設(shè)計方法。結(jié)論如下:(1)該方法能夠?qū)⑸拜喸O(shè)計的關(guān)鍵參數(shù)(磨粒尺寸、尺寸分布、粘結(jié)厚度等)和砂輪性能(磨粒突出狀況、微粘結(jié)力)關(guān)聯(lián)起來。(2)本研究建立了粘結(jié)厚度和磨粒突出、微粘結(jié)力之間的綜合關(guān)聯(lián)性。3.6μm粒度分布的#375金剛石砂輪的最佳粘結(jié)層厚度為24μm~33μm。(3)氧化鋁工程陶瓷材料的磨削實驗驗證了數(shù)字砂輪設(shè)計方法的有效性。(編譯:中國超硬材料網(wǎng))