磨削是一種結合了摩擦,耕犁和剪切并利用微粒進行材料磨除的多點切削工藝。通過砂輪速度、切削深度和工作臺速度等磨削參數(shù)的選擇可以加工出理想的工件。除了磨削參數(shù),修整參數(shù)對于被磨削產(chǎn)品的質(zhì)量也有著重要影響。修整是一種加工出適宜的砂輪表面形態(tài)的工藝過程;它包括修整導程、修整深度、修整角度和修整器刃尖半徑等參數(shù);其中修整導程和修整深度尤為重要。有研究就提出“磨削即修整”的說法。在實際工業(yè)生產(chǎn)中,通過頻繁地更換砂輪來滿足被磨削產(chǎn)品的質(zhì)量要求不太實際;此外,頻繁更換砂輪也會浪費大量時間從而增加整體生產(chǎn)成本。因此,為了得到一個較好的表面磨削和較高的材料磨除率,對特定磨料粒度的砂輪進行修整參數(shù)優(yōu)化就十分的必要。盡管有研究提出了磨粒粒度對表面光潔度和磨削力的影響,磨粒越大,表面粗糙度就越大,磨削力也就越大。但在實際生產(chǎn)實踐中,按照被磨削產(chǎn)品的要求用特定粒度的砂輪進行加工幾乎不太可能。本研究在眾多實驗研究的基礎上對修整導程和修整深度參數(shù)進行了討論研究。
本研究采用超合金英高鎳718進行實驗。英高鎳718熱強度高、抗腐蝕、抗蠕變性能好。表1是英高鎳718的機械性能參數(shù)。
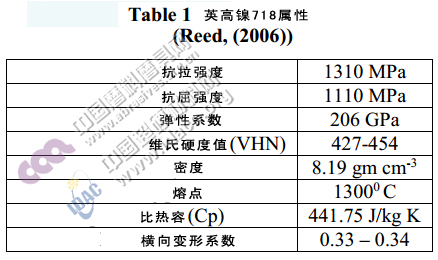
實驗
磨削實驗在Chevalier SMART-H1224兩軸CNC平面磨床上進行。英高鎳718試樣為100mm×70mm×10mm;砂輪速度18m/s,工作臺速度9m/min,磨削深度15μm,采用全因子分析方法選擇各種修整導程和修整深度。實驗采用兩個因子(修整導程和修整深度)和五個水平級。利用全因子分析法實驗共做了25組,修整導程值分別為50,150,250,350和450mm/min,修整深度為10,20,30,40,50μm。按照實驗具體設計對修整條件進行適時調(diào)整。實驗用單粒金剛石修整器進行修整,用切削冷卻液進行降溫處理。修整完畢再對試樣進行無火花磨削。隨后進行15μm深度的磨削,用壓電式測力計進行磨削力測定。所有磨削實驗都為順磨。采用白剛玉砂輪A60K5V。用泰勒霍布森輪廓儀在三個不同的位置測定表面粗糙度。所有Ra測定都采用橫向長度6mm,試樣長度0.8mm。
結果和討論
磨削力
圖1和圖2為法向磨削力和切向磨削力隨修整深度的變化。圖3和圖4為法向磨削力(Fn)和切向磨削力(Ft)隨修整導程的變化。從圖表中可以看出,修整導程對磨削力的影響要遠大于修整深度對其影響。
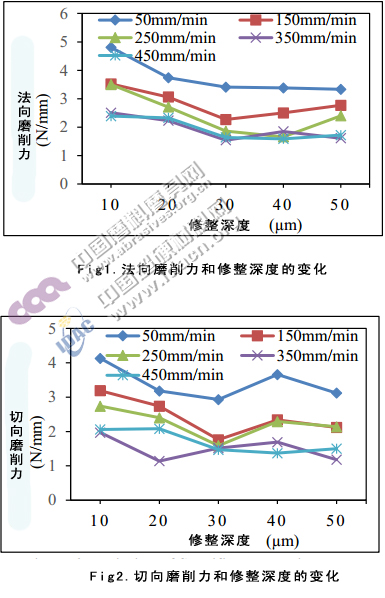
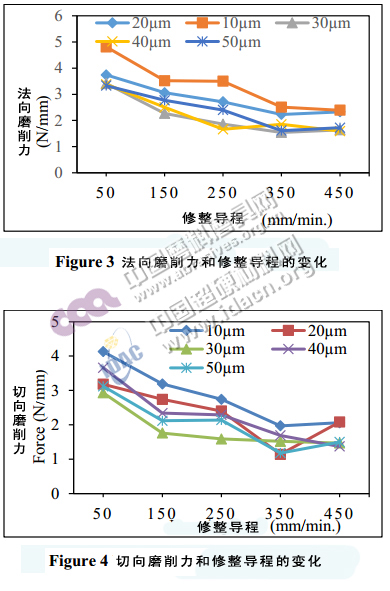
表面粗糙度
圖5為表面粗糙度隨修整導程的變化。細鑿修整下的工件表面更光滑,而粗糙修整下的粗糙度就很大。
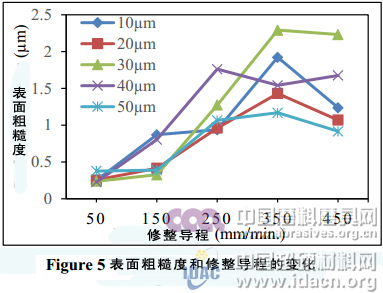
利用反應曲面分類研究法(RSM)對求得的法向磨削里(Fn)、切向磨削力(Ft)和表面粗糙度值進行分析;RSM結合數(shù)學和統(tǒng)計學技術用于建模和分析問題, 是一種反應曲面作為輸入變量的函數(shù)的序貫實驗程序。
由兩個因子和五個水平級求得的模型方程如下:
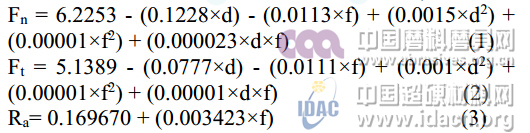
以上三個方程的R2值分別為92.3%、80.1%、59.2%,可以用來預測修整深度和修整導程的反應。表2為預測值和測量值之間的對比總結。實驗隨機挑選修整導程(f)和修整深度(d)。

未得到最優(yōu)化修整參數(shù)如最小表面粗糙度或者最小磨削力,實驗采用遺傳算法(GA)的優(yōu)化技術。在遺傳算法中,統(tǒng)計建模求得的方程式為適應度函數(shù),如式4、式5所示:

限制條件為:10≤X1≤50 50≤X2≤450
單極優(yōu)化的修整參數(shù)最佳水平為:

•從最左邊到最佳分區(qū)1,法向磨削力明顯下降,對應的表面粗糙度則上升。
•從優(yōu)化點到最右邊,(分區(qū)3),法向磨削力上升,對應的表面粗糙度則下降。
•最佳分區(qū)2:該分區(qū)表面粗糙度和法向磨削力的值都比較穩(wěn)定。
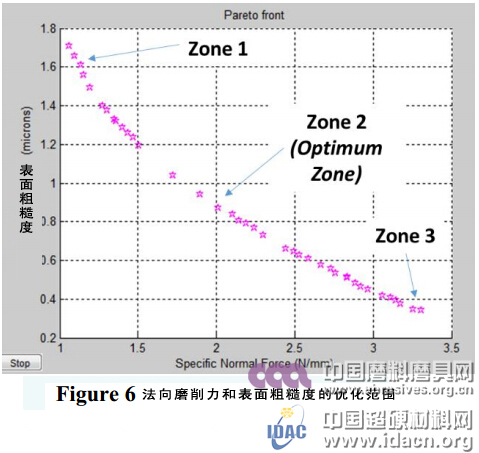
結論
本論文研究了剛玉砂輪(磨料粒度60)的修整深度和修整導程。得出以下結論:
1、磨削力(法向磨削力和切向磨削力)受修整深度影響比較顯著。對于最小磨削力,修整深度有一個最佳范圍30-40μm。
2、磨削力隨修整導程的增加而降低。本實驗最大修整導程為450mm/min時磨削力達到最小。
3、表面粗糙度只受修整導程影響修整導程越小,表面粗糙度就越低。本實驗修整導程最小為50mm/min時表面粗糙度最低。