眾所周知我們涂附磨具行業(yè)大家至今還在普遍沿用早在上個世紀(jì)80年代就已制定,1999年完成修訂的JB/T 10155-1999《砂布砂紙磨削性能試驗方法》標(biāo)準(zhǔn)和圓盤式砂紙磨削性能試驗機(jī)來測試砂帶的磨削性能。這對于實際工作時磨削線速度高達(dá)20—30m/s和強(qiáng)切削負(fù)荷的砂帶產(chǎn)品來說,實在是非常不適用。盡快制定適用于機(jī)械打磨的砂帶磨削性能測試方法已成為行業(yè)內(nèi)的一致呼聲。因此借試驗機(jī)試車的機(jī)會,以B公司的X產(chǎn)品為檢測對象進(jìn)行了一系列不同磨削條件的試驗,以期取得一些數(shù)據(jù)和經(jīng)驗,為制定砂帶磨削性能測試新規(guī)程提供參考和依據(jù)。
3.1 不同磨削壓力對砂帶磨削性能的影響
試驗共進(jìn)行了三次,分別測試了100N、150N和180N三種不同磨削壓力下的磨削性能,其他試驗條件如表3-1:
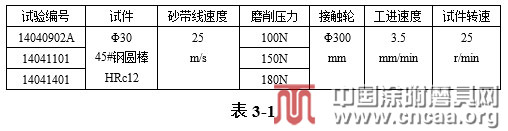
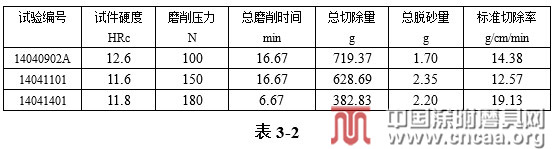
三個試驗?zāi)ハ髑谐亓康内厔輬D如圖3-1.
圖3-1表明,磨削壓力越高,在最初階段砂帶的磨削切除量也高;但隨著磨削的進(jìn)行,磨削壓力高,切除量下降的也越快。單次磨削切除量由首次的36.36g下降到第20次磨削的6.88g,切除量僅為第一次的19%,基本失去了使用價值,因此在180N壓力下的總切除量也是三次試驗中最低的一次,整個磨削過程磨削能力沒有相對穩(wěn)定的區(qū)域。而當(dāng)磨削壓力為100N時,盡管第一次的切除量為23.20g,是180N首次切除量的64%,可是磨削能力下降平緩,到第50次磨削的切除量仍為7.97g,是首次切除量的34%,而且總切除量達(dá)719.37g,是三次試驗中最大的。
可見磨削壓力對砂帶磨削性能的影響十分顯著;不同砂帶應(yīng)該有自己最適合的磨削壓力,過小的壓力無法得到理想的磨削效率,但過大的磨削壓力既得不到穩(wěn)定的磨削性能,也會造成砂帶的過早損壞??磥韺公司X產(chǎn)品的合適磨削壓力是在100-150N范圍內(nèi)。
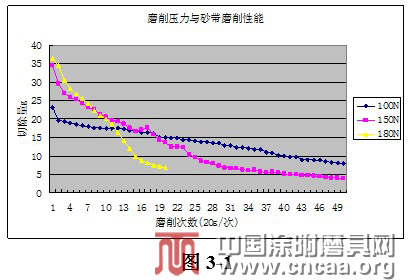
3.2不同工進(jìn)速度對砂帶磨削性能的影響
試驗共進(jìn)行了三次,分別測試了6mm/min、8mm/min和10mm/min 三種不同工進(jìn)速度下的恒進(jìn)給磨削性能,其他試驗條件如表3-3:
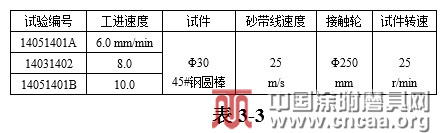
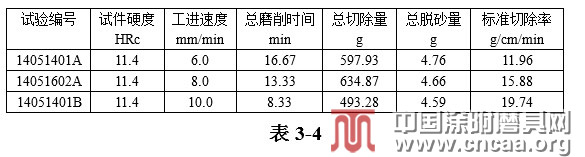
三個試驗?zāi)ハ鲏毫颓谐亓康内厔輬D如圖3-2,它表明:
1、在恒進(jìn)給磨削中,隨著工進(jìn)速度的提高,單次金屬切除量亦相應(yīng)增加;磨削壓力則隨著磨削次數(shù)的增加亦逐漸增加。工進(jìn)速度高的磨削壓力增加較快。在達(dá)到一定磨削次數(shù)后,磨削壓力出現(xiàn)迅速增加的趨勢,磨削溫度也急劇上升,工件出現(xiàn)燒傷,甚至?xí)鹕皫嗔选?br />
2、工進(jìn)速度為6mm/min時,恒定切除量的穩(wěn)定磨削區(qū)間長,整個試驗過程磨削壓力也十分平穩(wěn),未出現(xiàn)壓力變化的轉(zhuǎn)折點,表明這種工況下,砂帶的使用壽命會很長;在一定的時間里,金屬切除量能保持恒定,而壓力的增長緩慢,這樣的磨削區(qū)域在實際應(yīng)用中應(yīng)該是磨削的理想?yún)^(qū)。相反,工進(jìn)速度最高的10mm/min試驗,能保持恒定切除量的磨削時間很短,在第19次磨削就開始出現(xiàn)磨削壓力急劇上升的趨勢,到第25次磨削壓力已增大到第19次的3倍,失去了使用價值;雖然其標(biāo)準(zhǔn)切除率高,而總切除量是三次中最低的。
3、可見工進(jìn)速度在恒進(jìn)給磨削試驗中對砂帶磨削性能的影響十分顯著;不同砂帶應(yīng)該有自己最適合的工進(jìn)速度,過低的速度無法得到理想的磨削效率,但過高的速度既得不到穩(wěn)定的磨削性能,也會造成砂帶的過早損壞??磥韺τ贐公司X產(chǎn)品,采用6-8mm/min的工進(jìn)速度是比較合適的。
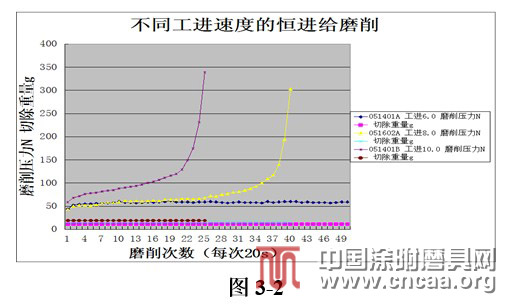
試驗共進(jìn)行了二次,分別測試了25m/s和35m/s二種不同線速度下的恒壓力磨削性能,其他試驗條件如表3-5:
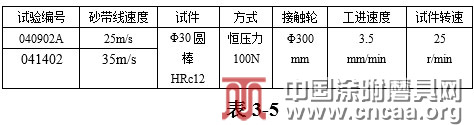
試驗結(jié)果如表3-6:
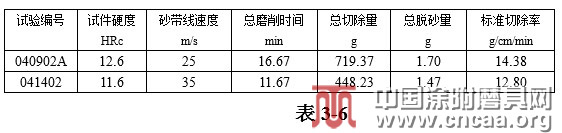
二個試驗切除重量的趨勢圖如圖3-3,它表明:
1,高的砂帶線速度,在磨削初始階段的金屬切除量要高于低的砂帶線速度,但隨著磨削次數(shù)的增加,切除能力下降很快。圖示35m/s在第9次磨削后的單次切除量迅速降低,明顯低于25m/s的切除量;到第26次磨削,單次切除量已下降到低于6g的水平。而25m/s直到第50次的切除量仍在8g以上??偳谐扛潜?5m/s高出60%。
2,初步分析認(rèn)為線速度高,磨削的滑擦作用顯著,耕犁作用減弱,致使磨粒的磨損加快,切削能力減小。此外線速度的高低也關(guān)系在單位時間內(nèi)參與磨削的磨粒數(shù)量,速度低參與的磨粒就少,這同樣不利磨削效率的提高。
3,試驗表明:不同類型的砂帶應(yīng)該有自己合適的砂帶線速度,對于B公司X產(chǎn)品采取25m/s是合適的。
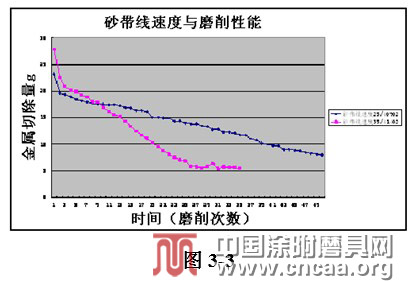
試驗共進(jìn)行了二次,分別測試了25r/min和35r/min二種不同試件轉(zhuǎn)速下的恒壓力磨削性能,其他試驗條件如表3-7:
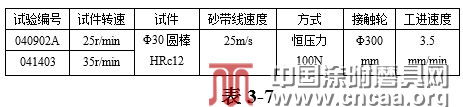
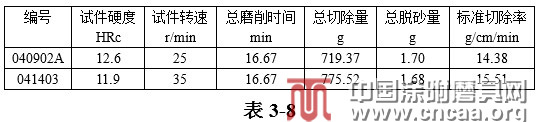
高的試件轉(zhuǎn)速確實促進(jìn)了總切除量的增加,與理論分析一致,因為試件轉(zhuǎn)速增加將提高工件圓周進(jìn)給速度,有利增加單位時間內(nèi)磨削的表面積;但是試驗數(shù)據(jù)顯示:速度提高了40%,而總切除量只增加了8%,估計是由于高的圓周速度會減少砂帶的耕犁作用,反而會影響磨削性能的下降。因此在上述兩種因素的綜合影響下,提高試件轉(zhuǎn)速對提高磨削效率的作用并不顯著。
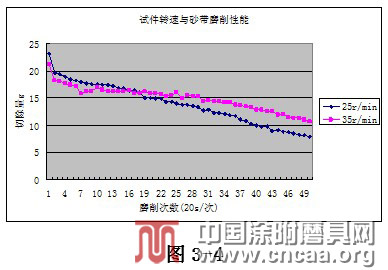
3.5 冷卻措施對砂帶磨削性能的影響
本試驗機(jī)沒有設(shè)置磨削冷卻的措施,但通過試車發(fā)現(xiàn)磨削冷卻十分重要,否則會造成試件的嚴(yán)重?zé)齻?,并影響砂帶磨削性能的發(fā)揮。為研究冷卻措施對磨削性能的影響,特選取了兩次試驗結(jié)果進(jìn)行對比,其中一次磨削時間為60s,未采取冷卻;另一次磨削時間為20s,同時采用壓縮空氣噴吹冷卻。其他試驗條件如表3-9:
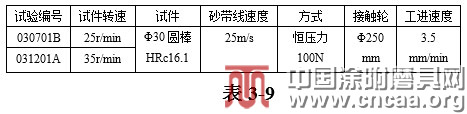
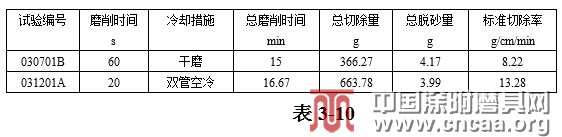
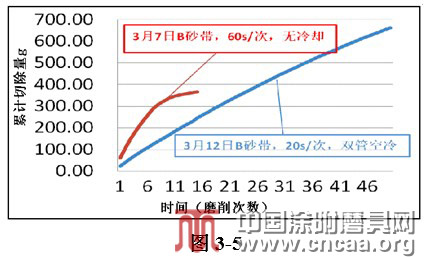
圖3-6為無冷卻磨削的實況;圖3-7為有冷卻磨削的實況。從圖3-6中可見磨削過程試件表面已變藍(lán),表明溫度已超過300°C,灼傷嚴(yán)重。而圖3-7所示試件表面正常。
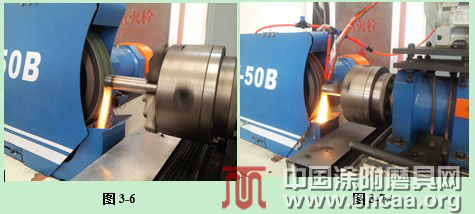
圖3-8為縮短磨削時間,增加噴氣冷卻后試件表面磨前、磨后的各次溫度情況,說明采取的措施是有效的。無冷卻措施時,由于溫度升高的很快,使砂帶的磨削能力下降也很快,磨削12min后,1min的切除量就已下降到6g左右,15min后僅為3g。當(dāng)采取縮短磨削時間,增加噴氣冷卻后,磨削16min后,20s的切除量仍高于9g;充分說明冷卻對磨削試驗的重要性。從總切除量的對比也可說明冷卻的重要,有冷卻要比無冷卻高出81%。
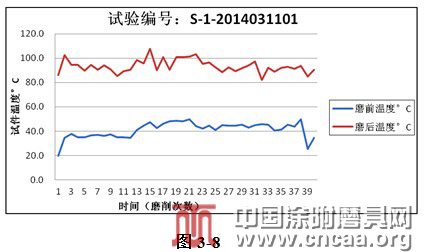
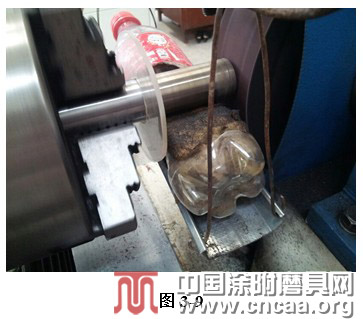