摘要 摘要:通過振動介質精磨工藝中表面輪廓隨加工時間的變化對表面形成機制進行研究;對表面輪廓中分線、峰值和谷值隨時間的變化進行檢測。峰高和谷深的降低說明材料從峰值到谷值發(fā)生了塑性位移。因...
摘要:
通過振動介質精磨工藝中表面輪廓隨加工時間的變化對表面形成機制進行研究;對表面輪廓中分線、峰值和谷值隨時間的變化進行檢測。峰高和谷深的降低說明材料從峰值到谷值發(fā)生了塑性位移。因此,表面形成機制可以看作是材料磨除和塑性形變的共同作用;這也說明了表面粗糙度的飽和隨時間的變化關系。
關鍵詞:
振動介質精磨,表面形成機制,表面輪廓,表面飽和
1、引言
磨損機制在改善零部件的表面光潔度加工工藝中十分常見,包括兩體模式和三體模式。兩體磨料加工有磨削、涂附磨具拋光等;把持牢固的磨料和工件表面相互作用。三體磨料加工則是自由磨粒線鋸切研磨;磨料被固定在襯墊和工件表面。三體磨料加工的一個典型工藝就是振動介質精磨,待拋光工件放入盛有介質顆粒的容器內(nèi)然后進行振動精磨;工件不和盛有介質的容器接觸,介質顆粒和工件相互接觸。介質顆粒為磨料結塊。容器可以盛下10公斤的介質顆粒。振動會引起介質顆粒發(fā)生一定形狀的運動并促使介質顆粒和工件表面接觸反應從而改變表面形態(tài)。
表面變化及其與時間的關系尚未研究清楚。利用振動介質精磨工藝得到的零部件表面粗糙度會隨著時間變化而飽和;一段加工時間之后,表面粗糙度就不再改善。因此,檢測出什么時候開始出現(xiàn)飽和有助于計算出加工次數(shù)。工件的質量變化在不同研究中存在較大差異。Hashimoto和Debra的研究得出持續(xù)增長的變化;Baghbanan等人的研究得出飽和結論;還有一些研究表明粗糙的工件表面比光滑的表面更能夠實現(xiàn)較大的材料磨除量。而導致表面粗糙度飽和的原因及其與介質顆粒的關聯(lián)性尚未明確。
通過振動介質精磨工藝中表面輪廓隨加工時間的變化對表面形成機制進行研究;對表面輪廓中分線、峰值和谷值隨時間的變化進行檢測。峰高和谷深的降低說明材料從峰值到谷值發(fā)生了塑性位移。因此,表面形成機制可以看作是材料磨除和塑性形變的共同作用;這也說明了表面粗糙度的飽和隨時間的變化關系。
關鍵詞:
振動介質精磨,表面形成機制,表面輪廓,表面飽和
1、引言
磨損機制在改善零部件的表面光潔度加工工藝中十分常見,包括兩體模式和三體模式。兩體磨料加工有磨削、涂附磨具拋光等;把持牢固的磨料和工件表面相互作用。三體磨料加工則是自由磨粒線鋸切研磨;磨料被固定在襯墊和工件表面。三體磨料加工的一個典型工藝就是振動介質精磨,待拋光工件放入盛有介質顆粒的容器內(nèi)然后進行振動精磨;工件不和盛有介質的容器接觸,介質顆粒和工件相互接觸。介質顆粒為磨料結塊。容器可以盛下10公斤的介質顆粒。振動會引起介質顆粒發(fā)生一定形狀的運動并促使介質顆粒和工件表面接觸反應從而改變表面形態(tài)。
表面變化及其與時間的關系尚未研究清楚。利用振動介質精磨工藝得到的零部件表面粗糙度會隨著時間變化而飽和;一段加工時間之后,表面粗糙度就不再改善。因此,檢測出什么時候開始出現(xiàn)飽和有助于計算出加工次數(shù)。工件的質量變化在不同研究中存在較大差異。Hashimoto和Debra的研究得出持續(xù)增長的變化;Baghbanan等人的研究得出飽和結論;還有一些研究表明粗糙的工件表面比光滑的表面更能夠實現(xiàn)較大的材料磨除量。而導致表面粗糙度飽和的原因及其與介質顆粒的關聯(lián)性尚未明確。
圖一:振動介質精磨工藝中隨時間變化的表面粗糙度和材料磨除
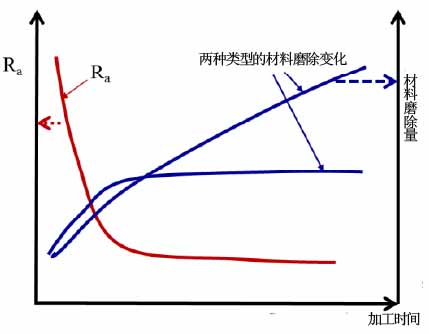
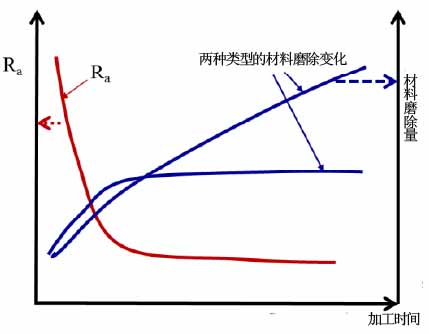
介質顆粒和工件表面的相互作用對表面形成機制有重要影響。Wang等人利用SEM分析對干式、濕式精磨工藝進行研究,實驗表明在干式精磨工藝中,材料磨除機制較為正常,濕式精磨工藝中出現(xiàn)刮痕磨損,這是由于濕式精磨中摩擦減小的緣故。Ciampini等人的研究也得出類似結論,同時還證實了旋轉機制。
對表面輪廓隨加工時間的變化進行檢測是研究表面峰值/谷值隨時間變化的另一種方法;這也是本論文所采用的實驗方法。利用檢測到的峰值/谷值變化來研究是否有材料磨除和材料移位發(fā)生,以及材料磨除量和壓痕類型數(shù)量。
如圖二所示,建立一個峰值/谷值易識別的結構表面輪廓,求得中分線并將其作為基線;由基線得到的峰高和谷深就可以記錄。在純材料磨除條件下只有峰值被磨蝕,得到的輪廓如圖2b所示。新的中分線將會向下移動;但原來的中分線求得的峰高和谷深可以看出是否有純材料磨除發(fā)生——只有峰高會發(fā)生變化。如果谷深也改變,如圖3b所示,則說明一定量的塑性移位發(fā)生;此時峰高的變化是由材料磨除或塑形壓痕所致。
對表面輪廓隨加工時間的變化進行檢測是研究表面峰值/谷值隨時間變化的另一種方法;這也是本論文所采用的實驗方法。利用檢測到的峰值/谷值變化來研究是否有材料磨除和材料移位發(fā)生,以及材料磨除量和壓痕類型數(shù)量。
如圖二所示,建立一個峰值/谷值易識別的結構表面輪廓,求得中分線并將其作為基線;由基線得到的峰高和谷深就可以記錄。在純材料磨除條件下只有峰值被磨蝕,得到的輪廓如圖2b所示。新的中分線將會向下移動;但原來的中分線求得的峰高和谷深可以看出是否有純材料磨除發(fā)生——只有峰高會發(fā)生變化。如果谷深也改變,如圖3b所示,則說明一定量的塑性移位發(fā)生;此時峰高的變化是由材料磨除或塑形壓痕所致。
圖二:(a)原始表面輪廓(b)純材料磨除發(fā)生時的表面輪廓(c)材料磨除和磨削耕犁發(fā)生時的表面輪廓
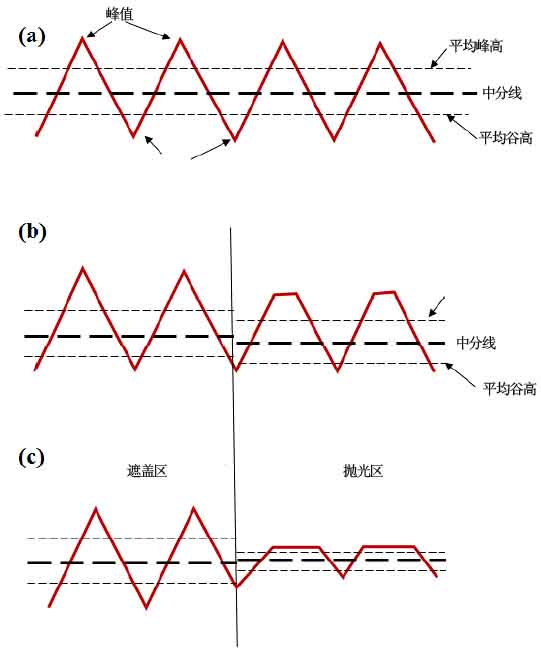
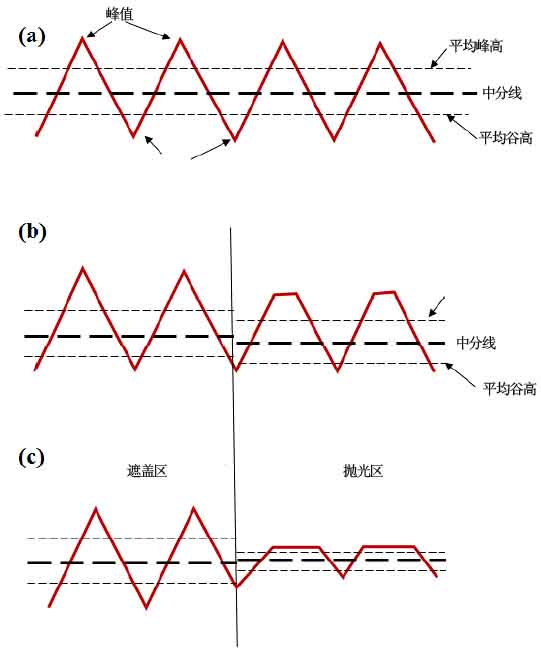
表一為觀察到的峰高和谷深變化
表一:表面輪廓變化
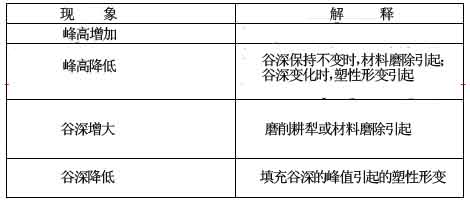
圖三:谷高降低的兩種途徑:(a)去除材料的碎屑被堆入谷底;(b)峰值的塑性形變被堆入內(nèi)部從而提高了谷值

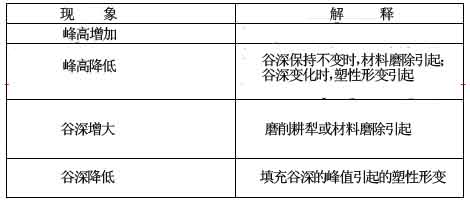
圖三:谷高降低的兩種途徑:(a)去除材料的碎屑被堆入谷底;(b)峰值的塑性形變被堆入內(nèi)部從而提高了谷值

2、檢測表面輪廓變化的實驗方法
檢測表面輪廓變化的兩個必要條件是:
1)表面峰值和谷值自始至終都統(tǒng)一一致:由于表面峰值和谷值的形狀、大小會影響表面改性的機制,因此,表面峰值和谷值如果不一致則會在表面的不同點上出現(xiàn)多個機制。
2)保留原始輪廓的中分線,以便對峰值和谷高的變化進行測量。
為實現(xiàn)第一個條件,在CNC銑床上利用飛刀對工件表面進行加工,高10μm,間隔150μm。刀尖圓角半徑為7-15微米,加工材料為鈦合金。為實現(xiàn)第二個條件,將工件表面的一部分遮蓋住,如圖四所示。
檢測表面輪廓變化的兩個必要條件是:
1)表面峰值和谷值自始至終都統(tǒng)一一致:由于表面峰值和谷值的形狀、大小會影響表面改性的機制,因此,表面峰值和谷值如果不一致則會在表面的不同點上出現(xiàn)多個機制。
2)保留原始輪廓的中分線,以便對峰值和谷高的變化進行測量。
為實現(xiàn)第一個條件,在CNC銑床上利用飛刀對工件表面進行加工,高10μm,間隔150μm。刀尖圓角半徑為7-15微米,加工材料為鈦合金。為實現(xiàn)第二個條件,將工件表面的一部分遮蓋住,如圖四所示。
圖四:遮蓋住工件表面的一部分以保留原始中分線。在遮蓋區(qū)和非遮蓋區(qū)進行表面輪廓痕跡測量
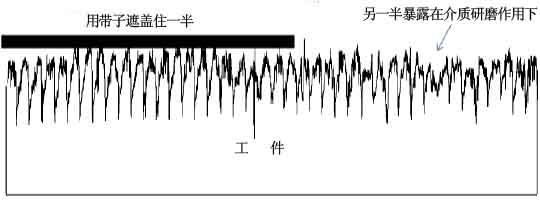
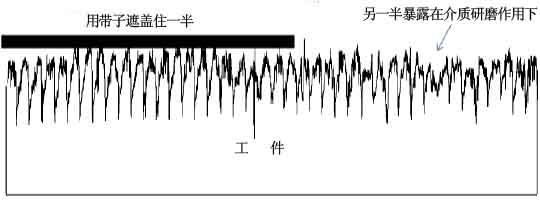
步驟如下:
1)計算遮蓋部分上半部輪廓平均值,作為遮掩基準線的高度;
2)計算遮蓋部分下半部輪廓的平均值,作為分析基準線的高度;
3)分析基準線以上的值為峰值;
4)分析基準線以下的值為谷值;
5)計算遮掩基準線和峰值之間的差值,將其作為峰高;計算峰高的平均值;
6)計算遮掩基準線和谷值之間的差值,將其作為谷深;計算谷深的平均值。
和其他測量技術一樣,該技術也會有一定的誤差。通過分析誤差并將其列入結果分析,就可以避免數(shù)據(jù)丟失和數(shù)據(jù)誤解。通過對工件表面的精銑加工可以得到整齊的峰值和谷值;由于任何加工工藝都存在公差范圍,所以,實驗結果可以允許公差的存在。但利用遮蓋參考基準的方法則可以消除這個問題——每一次記錄遮蓋基準線時尺寸變化就會被記錄。因此,波紋、公差誤差引起的表面尺寸變化就會被消除。根據(jù)新等分線隨時間的變化計算出峰值和谷值,一些點可能會存在曲解,比如當峰值和谷值都向原始中分線移動時,新的中分線就會下降,而新的谷值位置可能保持不變。這意味著發(fā)生了塑性形變,但在計算中不會體現(xiàn)出來。
在表面5個不同點上測量表面輪廓,振動精磨過程中每隔20分鐘進行一次峰高和谷深變化的計算。利用Taylor Hobson Formtracer測量表面輪廓。每隔20分鐘將工件拿出進行表面輪廓測量和SEM測量。
3、結果和討論
利用表面粗糙度參數(shù)Ra對表面變化進行量化如圖5所示,可以看出明顯的表面粗糙度飽和。加工間隔出現(xiàn)的Ra變化說明隨時間單調(diào)遞減。峰高和谷深隨時間變化如圖6所示。峰高單調(diào)遞減并達到飽和;谷深也降低并達到飽和。在接近100分鐘加工時間時,峰高飽和、谷深飽和和表面粗糙度飽和都得以實現(xiàn)。圖6可以明顯看到整個工藝不僅是單次磨損的峰值,還伴隨著谷深的降低。
1)計算遮蓋部分上半部輪廓平均值,作為遮掩基準線的高度;
2)計算遮蓋部分下半部輪廓的平均值,作為分析基準線的高度;
3)分析基準線以上的值為峰值;
4)分析基準線以下的值為谷值;
5)計算遮掩基準線和峰值之間的差值,將其作為峰高;計算峰高的平均值;
6)計算遮掩基準線和谷值之間的差值,將其作為谷深;計算谷深的平均值。
和其他測量技術一樣,該技術也會有一定的誤差。通過分析誤差并將其列入結果分析,就可以避免數(shù)據(jù)丟失和數(shù)據(jù)誤解。通過對工件表面的精銑加工可以得到整齊的峰值和谷值;由于任何加工工藝都存在公差范圍,所以,實驗結果可以允許公差的存在。但利用遮蓋參考基準的方法則可以消除這個問題——每一次記錄遮蓋基準線時尺寸變化就會被記錄。因此,波紋、公差誤差引起的表面尺寸變化就會被消除。根據(jù)新等分線隨時間的變化計算出峰值和谷值,一些點可能會存在曲解,比如當峰值和谷值都向原始中分線移動時,新的中分線就會下降,而新的谷值位置可能保持不變。這意味著發(fā)生了塑性形變,但在計算中不會體現(xiàn)出來。
在表面5個不同點上測量表面輪廓,振動精磨過程中每隔20分鐘進行一次峰高和谷深變化的計算。利用Taylor Hobson Formtracer測量表面輪廓。每隔20分鐘將工件拿出進行表面輪廓測量和SEM測量。
3、結果和討論
利用表面粗糙度參數(shù)Ra對表面變化進行量化如圖5所示,可以看出明顯的表面粗糙度飽和。加工間隔出現(xiàn)的Ra變化說明隨時間單調(diào)遞減。峰高和谷深隨時間變化如圖6所示。峰高單調(diào)遞減并達到飽和;谷深也降低并達到飽和。在接近100分鐘加工時間時,峰高飽和、谷深飽和和表面粗糙度飽和都得以實現(xiàn)。圖6可以明顯看到整個工藝不僅是單次磨損的峰值,還伴隨著谷深的降低。
圖5:(a)表面粗糙度Ra隨加工時間變化;(b)Ra百分比變動
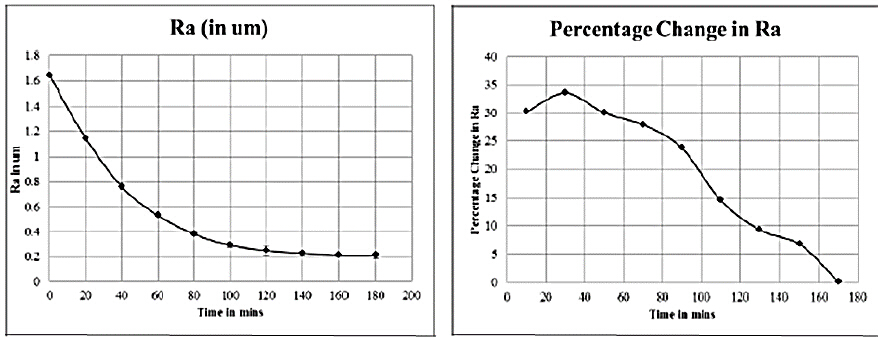
圖6:峰高、谷深隨時間變化

圖7:谷深變化作為塑性形變的分析
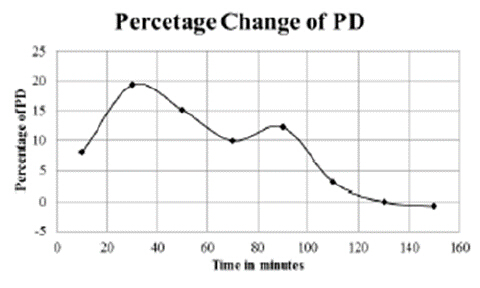
圖8:不同加工時間間隔下的表面SEM
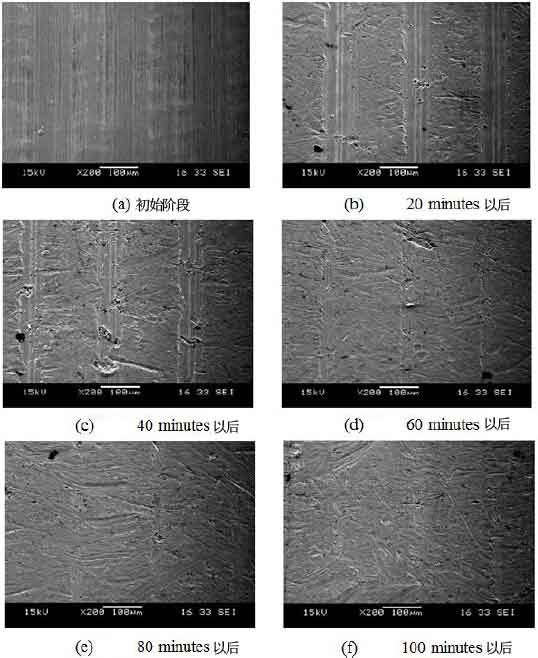
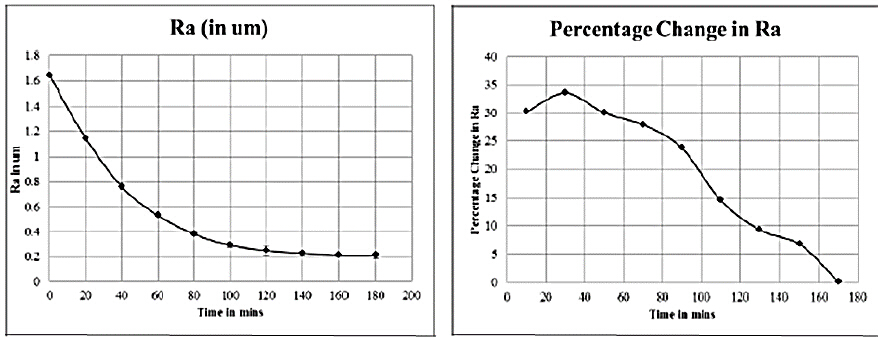
圖6:峰高、谷深隨時間變化

圖7:谷深變化作為塑性形變的分析
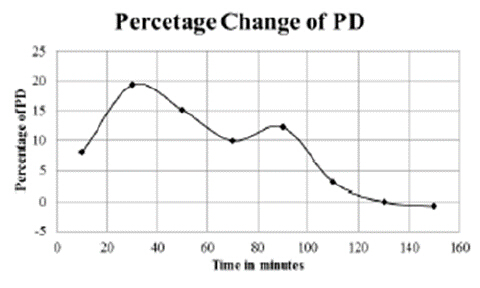
圖8:不同加工時間間隔下的表面SEM
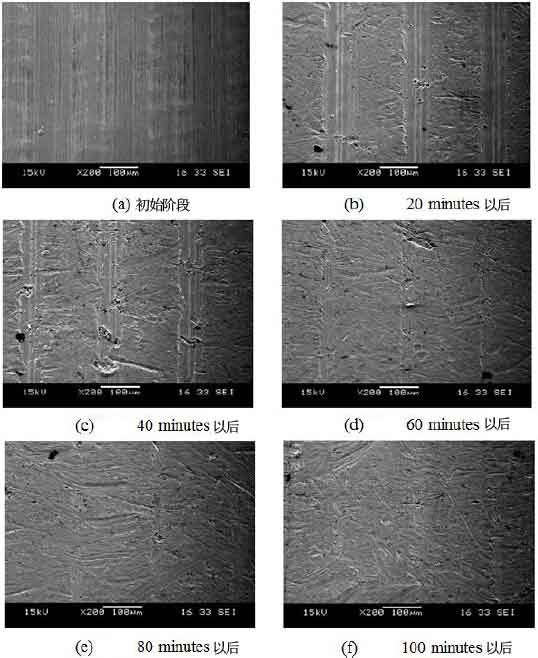
圖8a為加工之前的表面形態(tài)SEM圖;8b為精磨20分鐘之后的SEM圖。由此可以看出,經(jīng)過精磨工藝的表面修補得到了改性,這些修補也即結構性表面的峰值區(qū)。峰值在初期被改性,留下谷值保持不變。這在圖8b的20分鐘時間間隔中峰值和谷值的高度變化上也可以反映出來。8c為40分鐘后表面形成的SEM圖,8d為60分鐘表面形成的SEM圖。由此可以看出,40分鐘后,谷值開始受到介質的影響;同時表面出現(xiàn)劃痕,說明劃痕比塑性形變更能引起更大的材料磨除。在8c中也有此類反映,初期的塑性形變總量要比材料磨除小許多。60分鐘后,谷值寬度緩慢減小。如果是材料磨除引起了表面形態(tài)的變化,那么谷深將增大。但表面輪廓測量顯示,谷深寬度是減小的;這說明峰值發(fā)生了塑性形變并被推入谷值。80分鐘后(如圖8e所示),谷值基本全部形變;100分鐘后(如圖8f所示),峰值和谷值基本沒有明顯區(qū)分。
4、結論
通過不同時間間隔下對比表面輪廓蹤跡,論文對振動介質精磨工藝中的表面變化進行了研究。得出以下結論:
表面粗糙度參數(shù)Ra隨加工時間最終飽和;
峰高隨加工時間單調(diào)遞減,說明材料磨除或峰值推進下降;
谷深隨加工時間單調(diào)遞減,說明塑性形變引起谷值增大;
表面粗糙度參數(shù)飽和時,峰高和谷深也同時飽和;
飽和可以看作是介質不能再繼續(xù)填入或研磨峰值并引起谷值增加。
(編譯:中國超硬材料網(wǎng)) 4、結論
通過不同時間間隔下對比表面輪廓蹤跡,論文對振動介質精磨工藝中的表面變化進行了研究。得出以下結論:
表面粗糙度參數(shù)Ra隨加工時間最終飽和;
峰高隨加工時間單調(diào)遞減,說明材料磨除或峰值推進下降;
谷深隨加工時間單調(diào)遞減,說明塑性形變引起谷值增大;
表面粗糙度參數(shù)飽和時,峰高和谷深也同時飽和;
飽和可以看作是介質不能再繼續(xù)填入或研磨峰值并引起谷值增加。