關(guān)鍵詞:
工業(yè)陶瓷,磨料研磨,表面精整,磨除材料總量
引言
陶瓷是一種由元素周期表III-VI族中的非金屬和金屬化合物構(gòu)成的多晶材料及制品;通過對源材料的燒制和成型加工制備而成。天然形成的化合物如硅酸鹽、粘土和石英以及人造陶瓷(高純氧化物、碳化物和氮化物等)都可以用作源材料。
工業(yè)陶瓷在機械工程領(lǐng)域廣泛應(yīng)用于結(jié)構(gòu)性耐高溫耐火零部件,如器材殼體、坩堝、齒輪和渦輪葉片的生產(chǎn);還用于儀器儀表和化學(xué)工業(yè)中環(huán)境較為惡劣的條件下的使用。
陶瓷的機械加工是一種繁瑣費力的加工工藝,旨在實現(xiàn)加工零部件的所需精度和工件表面質(zhì)量要求;其加工方法有下述幾種:
i.磨料研磨
ii.電火花、電化學(xué)加工
Iii.超聲波加工
iv.水動力加工
v.激光切割
陶瓷機械加工常見工藝有磨削和精整(Breev B.T. 1982, Antyufeeva T.P. 1999)。
天然及人造剛玉、碳化硅和碳化硼等材料常用于陶瓷的磨削和精整;而金剛石拋光則常用于鍺、硅、玻璃、石英和固態(tài)合金的加工處理。金剛石拋光工藝具有磨損小,工具耐用性高的優(yōu)點。根據(jù)日本研究者的實驗數(shù)據(jù),陶瓷拋光的成本費用是結(jié)構(gòu)鋼精整加工的成本費用的10倍之高(A.P. Garshin 2003, J. Kang, 2005, Jeong-Du Kim, 1995)。
陶瓷材料的性能如硬度、脆性、強度、多孔性、表面態(tài)、熱穩(wěn)定性,以及磨料屬性和所用刀具等都會影響陶瓷的機械加工;而陶瓷切削速度、夾持力和拋光材料的冷卻等加工條件也會影響陶瓷的機械加工。一般情況下,陶瓷的機械研磨由三步驟工藝流程:粗加工、清潔處理和精加工。
第一步,利用大粒度工具磨除80%左右的材料并以漸增速度進行磨削加工處理;該處理工藝會在工件表面產(chǎn)生較深的裂縫和損傷。工件尺寸的粗公差可達0.3-0.5mm;根據(jù)零部件的尺寸,可分為單面和雙面。第二步,利用小粒度研磨工具進行磨削加工并降低磨除材料量。第三步,利用金剛石微粉和研磨膏進行精整加工,達到標(biāo)稱尺寸。該步驟工藝完成后通常要進行拋光處理,以達到1-3級的精度要求和較低的表面粗糙度。
陶瓷表面的裂紋類型隨著不同的磨削工藝步驟而不同。在金剛石粗加工階段,脆性破壞導(dǎo)致的裂紋為主要類型。實驗觀察到兩種脆性損傷,一種是研磨工具夾持力導(dǎo)致的裂縫,另一種是陶瓷和磨料的相對運動產(chǎn)生的切向力引起了粘結(jié)相,進而導(dǎo)致晶體(磨粒)發(fā)生分離(剝落)。
在上述作用力的影響下,金剛石磨粒上會發(fā)生局部磨損,磨粒面會出現(xiàn)鈍化或裂縫。粗加工之后,這些缺陷會保留在其表面。這些缺陷的數(shù)量取決于金剛石磨粒的屬性、尺寸和形狀等。清潔拋光工藝中使用小粒度的研磨工具,進而減少了脆性開裂;該階段研磨影響和塑性變形為主要因素。陶瓷表面呈壓扁狀。在精整工藝中,利用小粒度的金剛石微粉和研磨膏進行加工處理,研磨影響為主要因素。工件表面精度為1-4級(Baharev B.P. 2009, Vakser D.B.. 1986)。
因此,利用磨削工藝對陶瓷工件進行機械加工是一個復(fù)雜的工藝,它取決于陶瓷材料的屬性、磨削參數(shù)、拋光參數(shù)和其他因素等。本文則研究了VSH-75(HRC90-93)陶瓷試樣的拋光加工;并將其硬度、熱穩(wěn)定性和耐磨性與硬質(zhì)合金進行對比。VSH-75陶瓷的缺陷是強度低,脆性高。裝配著VSH-75陶瓷片的設(shè)備器械可以在高達1200°Ñ的加工條件下保持其硬度不變。VSH-75陶瓷可用于無應(yīng)力、高速高溫條件下鑄鐵、鋼部件、有色金屬及其合金加工處理的清潔、半清潔拋光工藝。
材料及實驗方法
精加工實驗所用研磨機型號為Raster220,專業(yè)精加工各種機械零部件高精平面。這種桌式機床有三大部分構(gòu)成:傳送、沖壓和帶有變頻器的控制面板。
磨料為電熔白剛玉、綠碳化硅和人造金剛石粉末。金剛石粒度為40-5μm,每個工序中都有其樣品說明。利用過濾法將磨料均勻沉積在研磨平面上。
不考慮磨料自身的屬性,所有實驗中磨料的體積均設(shè)置為50cm3。該體積參數(shù)可以在直徑為220mm的研磨表面形成單層磨料沉積層。 根據(jù)其體積與比重,計算求得每種微粉的重量:
• 綠碳化硅-160mg;
• 人造金剛石-175mg;
煤油(70%)、烯酸(25%)和石油(25%)混合液做實驗的液相環(huán)境。將0.75-1cm3p體積的混合液滴在研磨表面上。
實驗結(jié)果
在裝配有軌跡掃描工具(Khanov A. M. 2010,Antsiferov V.N.. 2011,Nekrasov V.P. 2006, KhanovA..2010)的研磨機上對VSH-75(HRC90-95)材料制備而成的工件進行研磨加工。研磨工具材料為珠光體鑄鐵SCH28。所需表面粗糙度低于0.9μm.
磨料微粉的屬性對研磨精加工的結(jié)果有著很大的影響,特別是對陶瓷等硬質(zhì)材料的精加工。利用鑄鐵研磨工具,采用電熔白剛玉EB M400、綠碳化硅KZ M40和人造金剛石ASM40微粉磨料進行精加工的對比實驗就證明了這一點。通過每隔4分鐘計算材料去除總量可知:人造金剛石微粉ASM40的效率是EB M40和KZ M40效率的15-30倍(如圖一a所示)。這是由于加工材料的硬度略低于微粉EB M40和KZ M40,而人造金剛石ASM40的硬度則明顯高于陶瓷的硬度。工件表面粗糙度基本不受磨料類型影響,其變化在誤差范圍內(nèi)(圖一b)。
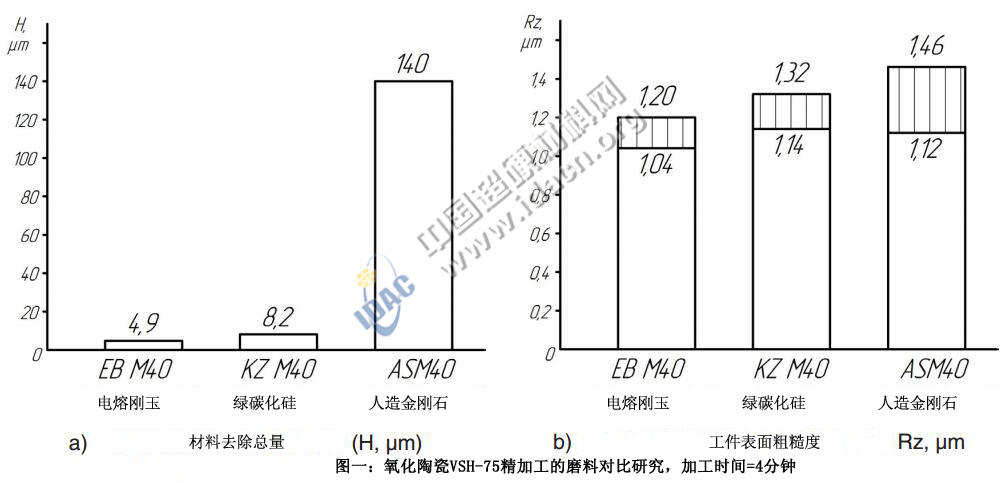
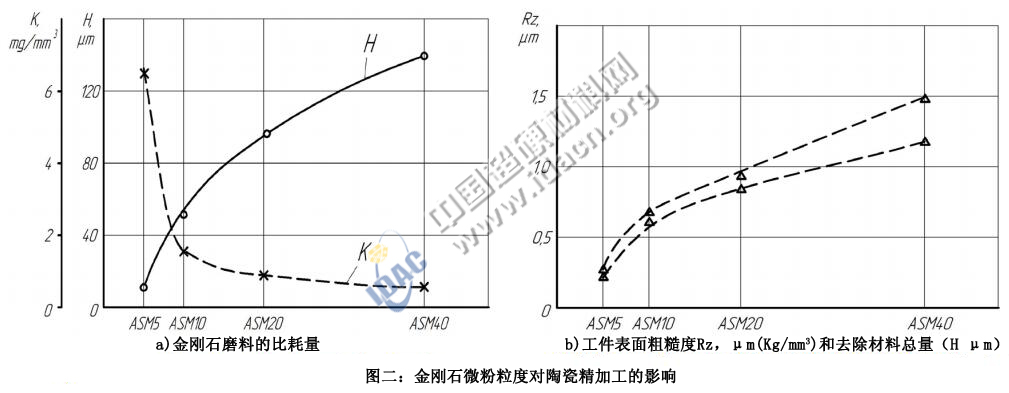
研磨表面的金剛石微粉量會影響精加工的性能、金剛石的單位消耗量K和加工效率H。在金屬-陶瓷材料加工實驗中,金剛石微粉ASM20的數(shù)量變化范圍為50-175mg。
金剛石相對比耗量和材料去除總量隨金剛石微粉量的增加而增加,如圖三所示。
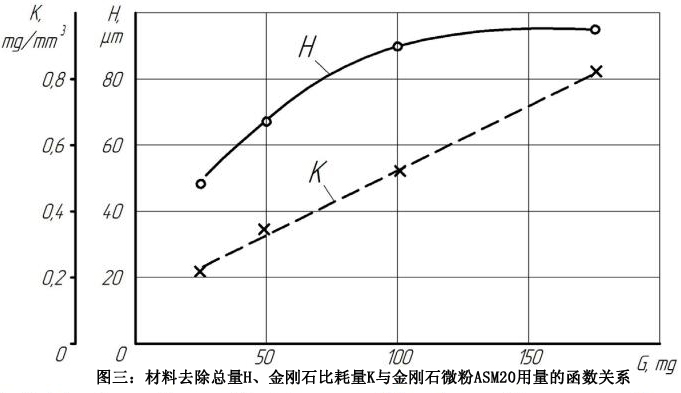
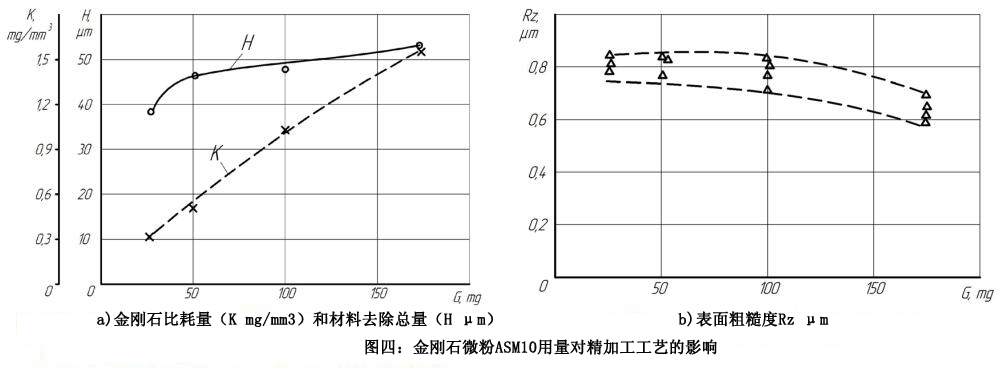
利用鑄鐵研磨工具CHS-28對金屬-陶瓷工件進行精加工時,金剛石微粉ASM10和ASM20的最佳用量分別為20-45mg,40-80mg。
工件和研磨工具的接觸壓力通過金剛石磨粒得以傳遞。在25-150kPa壓力范圍內(nèi),利用ASM20磨料對陶瓷精加工過程中接觸壓力的影響研究表明:材料去除總量隨著接觸壓力由25增大至50kPa而增大;當(dāng)壓力增至150kPa時,去除總量略有增加(圖五a)。后者這種增加不甚明顯的情況主要是由于高負荷下金剛石微粉磨粒的精煉所致。金剛石磨料的比耗量(k)隨壓力增大而降低,最為明顯的降低發(fā)生在25-50kPa壓力范圍內(nèi)(圖五a)。
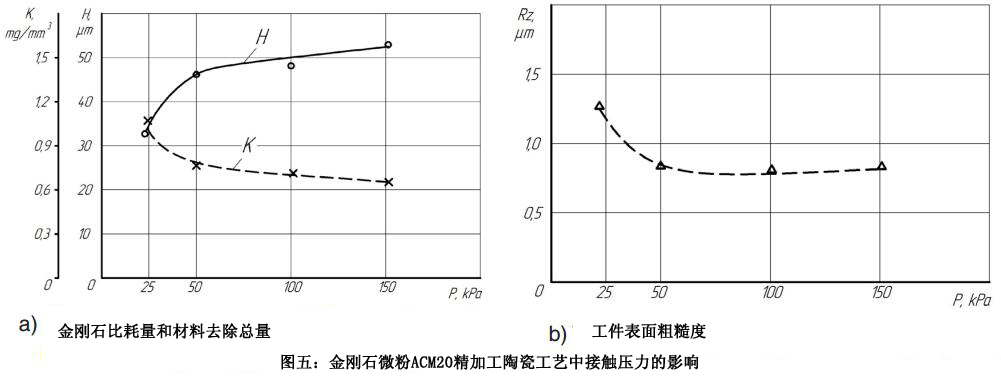
結(jié)論
人造金剛石微粉的粒度顯著影響加工表面的粗糙度和精整效率。去除材料總量和表面粗糙度隨粒度增大而增大。為滿足Rz=0.9μm的要求和高效加工,推薦采用ASM20人造金剛石微粉。
研磨工具和工件的接觸壓力也會影響精加工。接觸壓力由25 kPa增至50 kPa時,材料去除總量顯著增加,金剛石磨料的比耗量和工件表面粗糙度則降低。但隨著接觸壓力進一步增大至150 kPa,接觸壓力的影響則不再明顯。鑄鐵研磨工具CHS-28精加工陶瓷材料時的最佳接觸壓力為50-100kPa。(編譯:中國超硬材料網(wǎng))