最近的研究表明,多相復合陶瓷材料是未來先進結構陶瓷材料的三大發(fā)展趨勢之一。同樣,陶瓷材料向多相復合方向發(fā)展,為陶瓷刀具材料的設計、制造與應用提供了更寬的思考余地。本文以筆者所研制的新型多相復合陶瓷刀具材料Al2O3/SiC/(W,Ti)C為基礎,詳細研究了該刀具材料在切削鑄鐵時的磨損性能與磨損機理,為新型陶瓷刀具材料的進一步推廣應用奠定了良好的基礎。
1.試驗條件
切削試驗在CA6140機床上進行,工件材料為灰口鑄鐵HT300,硬度為200~250HB。所用刀具材料為Al2O3/SiC/(W,Ti)C多相復合陶瓷刀具材料,以ASW表示。為便于對比分析,同時采用了Al2O3/SiC和Al2O3/(W,Ti)C兩相復合陶瓷刀具材料,并分別以AS和AT表示。刀具幾何角度均為g0=-5°,a0=5°,ls=-5°,kr=75°,bg1×g01=0.2mm×(-20°),re=0.6mm。刀具磨損面的微觀結構觀察在HITACHIS-570型掃描電鏡上進行。幾種陶瓷刀具材料的力學性能如表所示。
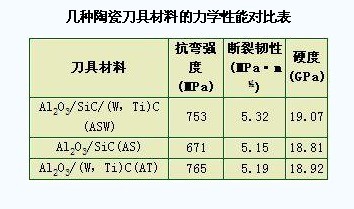
圖 1a為幾種陶瓷刀具材料在v=100m/min,f=0.2mm/r,ap=5.0mm的切削條件下切削灰口鑄鐵時的后刀面磨損曲線。由此可見,幾種陶瓷刀具材料均具有良好的耐磨性能,其中以ASW刀具為最好,AT刀具次之,而只含SiC的氧化鋁系陶瓷刀具材料AS的耐磨性能最差。在本試驗條件下,幾種陶瓷刀具材料的后刀面磨損比較均勻,磨損曲線均較好地符合磨損規(guī)律。與此相對比,在較高的切削速度和較小的切削深度條件下 (v=230m/min,f=0.2mm/r,ap=2.5mm)(圖1b),幾種陶瓷刀具材料的磨損規(guī)律雖與此類似,但磨損性能不同。按照后刀面磨損性能的優(yōu)劣,其順序為AT優(yōu)于ASW優(yōu)于AS。相對而言,組分的不同對材料耐磨性能的影響更加明顯。此外,對比圖1a和1b還可以看出,在后者的切削條件下,切削相同時間時相應刀具材料的后刀面磨損量較大。而且刀具材料不同,磨損量的增大程度也有所不同。對于ASW陶瓷刀具材料,在圖1a和1b兩種切削條件下的最大后刀面磨損量從0.28mm增大到0.40mm。而對于AS和AT陶瓷刀具材料,則分別從0.36mm和0.31mm增大到0.52mm和 0.35mm。
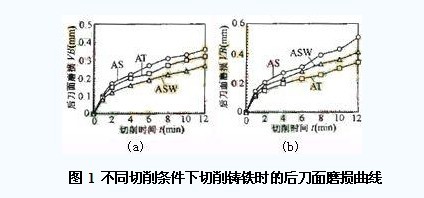
陶瓷刀具在低速下切削鑄鐵時的刀具磨損形式為前刀面和后刀面磨損,主要磨損機理為磨粒磨損。研究表明:對于以磨粒磨損機制為主的陶瓷等脆性材料,其抗磨損能力與KIC?H?成正比。斷裂韌性KIC越高,硬度H越高,材料的耐磨性能就越高。而由上表可見,ASW陶瓷刀具材料的斷裂韌性和硬度均高于其它兩種刀具材料AS和AT,因此其抗磨損性能最好。另一方面,在低速切削鑄鐵時,由于切削溫度較低,材料內(nèi)部的SiC還不至于與Fe發(fā)生化學反應,而且SiC本身也不至于產(chǎn)生氧化或氧化很微弱。此時粘結磨損、化學反應和氧化磨損所占的比例較小,因此含SiC和ASW陶瓷刀具材料表現(xiàn)出良好的耐磨性能。圖2為ASW陶瓷刀具材料后刀面磨損的SEM形貌,從中可以發(fā)現(xiàn)明顯的磨粒磨損的痕跡,而粘結現(xiàn)象很輕微。
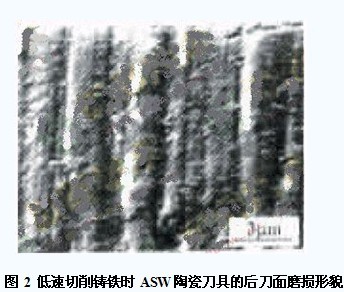
但在高的切削速度下,雖然刀具的磨損形式也多以前刀面和后刀面磨損為主,但前刀面磨損區(qū)中的粘結現(xiàn)象大大增加。圖3a為ASW陶瓷刀具材料的前刀面磨損形貌。由于切削時的高溫作用,SiC與Fe發(fā)生化學反應的趨勢增大,粘結磨損加劇。另一方面,在高溫下還會產(chǎn)生溶解磨損。研究發(fā)現(xiàn),在高溫下Fe在SiC中的溶解度比在TiC等中的溶解度高約2個數(shù)量級以上。因此,由于Fe與SiC 的化學反應及其相互溶解,使刀具中Fe元素的含量增加。這將增大刀具與工件材料的粘結傾向,因而對刀具的耐磨性能不利。同樣,后刀面粘結現(xiàn)象的增加也證明了這一點(圖3b)。
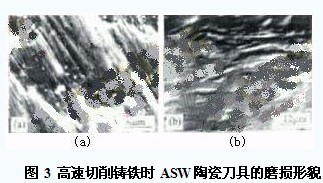
事實上,含SiC的陶瓷刀具材料在高速加工鐵族類工件材料時都存在這一問題。因此,在選擇刀具材料時必須加以注意??梢钥紤]將它用于低速大切深等粗加工工序中,或者在加工鎳基合金時采用,因為含SiC的陶瓷刀具材料在切削純鎳或鎳基合金時表現(xiàn)出良好的切削性能。此外,可以在設計新型陶瓷刀具材料時就考慮到工件材料與刀具材料的相容性問題,從而有針對性地制造出專門用于某一類或某幾類工件材料加工的刀具材料。