本文就汽車復(fù)合材料的涂裝、連接、維修和回收等四大應(yīng)用技術(shù)問(wèn)題進(jìn)行探討,以其拋磚引玉。
汽車復(fù)合材料的涂裝
在汽車工業(yè)中,汽車車身的外表油漆質(zhì)量是整車質(zhì)量最重要的指標(biāo)之一,因?yàn)檐嚿碛推岜砻娌粌H起到保護(hù)車廂不被腐蝕的作用而且對(duì)汽車美化外觀有著十分重要的影響。因此,盡管汽車生產(chǎn)主機(jī)廠承認(rèn)復(fù)合材料與傳統(tǒng)的金屬相比具有種種的優(yōu)點(diǎn),但是他們對(duì)于復(fù)合材料經(jīng)噴涂后的表面是否具有同金屬表面一樣的質(zhì)量,仍持保留態(tài)度。事實(shí)上,復(fù)合材料在汽車車身面板方面使用中所遇到的一個(gè)最大的挑戰(zhàn)就是:復(fù)合材料經(jīng)涂裝后產(chǎn)生的瑕疵。
我們以復(fù)合材料在汽車車身面板方面使用最多的片狀模塑料SMC部件為例,SMC車身部件在涂裝后通常會(huì)產(chǎn)生很多的表面瑕疵,例如:針眼、氣孔、裂紋、氣泡等,尤其在車身面板的邊緣區(qū)域氣泡情況較為嚴(yán)重。為了彌補(bǔ)這些缺陷,減少不合格產(chǎn)品率,提高部件的表面質(zhì)量,國(guó)內(nèi)生產(chǎn)廠家目前是通過(guò)大量的涂裝后修補(bǔ)手段如破泡、打磨、填膩?zhàn)?、拋光等?lái)加以改進(jìn),然后再按通常的涂裝工藝進(jìn)行表面再涂裝。這樣做的結(jié)果雖然減少了不合格品率,但增加了大量的后修補(bǔ)工序和再涂裝使生產(chǎn)成本大幅上升,另外也限制了SMC在A級(jí)車身面板上的應(yīng)用。
SMC車身面板在涂裝后產(chǎn)生表面油漆瑕疵和起泡的原因絕大部分都?xì)w因于基質(zhì)中的微小孔隙和微裂紋。而這些微小孔隙和微裂紋常常是在生產(chǎn)及搬運(yùn)過(guò)程中不注意人為形成的,例如從部件的模壓到脫模到除邊的過(guò)程,以及從部件的包裝到運(yùn)輸?shù)倪^(guò)程,我們經(jīng)常會(huì)發(fā)現(xiàn),在部件的邊緣部分會(huì)產(chǎn)生許多微裂紋。正是這些看似微不足道的微小孔隙和微裂紋,在油漆噴涂過(guò)程中積聚了空氣中的水分和油漆中揮發(fā)性溶劑,當(dāng)油漆后的SMC部件通過(guò)烘箱高溫烘烤時(shí),水分和溶劑膨脹蒸發(fā)變成氣泡逸出,造成已噴完漆的部件表面起泡或氣泡破裂變成氣孔、針眼等油漆瑕疵。
就SMC部件在涂裝后產(chǎn)生的表面瑕疵,目前國(guó)外復(fù)合材料行業(yè)主要的做法是消除微孔隙和微裂紋,從根夲上杜絕產(chǎn)生油漆表面瑕疵的根源,收到了很好的效果,主要有以下幾方面的措施:
1. 生產(chǎn)高強(qiáng)度、高韌性SMC樹(shù)脂。
近年來(lái),美國(guó)AOC公司和Thyssenkrupp Budd 公司聯(lián)合起來(lái)開(kāi)發(fā)了Atryl® TCA一種新的SMC樹(shù)脂。這種SMC樹(shù)脂強(qiáng)度高,生產(chǎn)出的部件可減少50%的表面波痕(與傳統(tǒng)的SMC表面相比),并增加了69%的韌性(與傳統(tǒng)的SMC樹(shù)脂相比)。由于具有這些性能,可顯著地阻止在脫模過(guò)程及脫模后微裂紋的產(chǎn)生,這樣即使在重要的邊緣區(qū)域也不會(huì)產(chǎn)生微裂紋。
2. 加強(qiáng)模壓工藝控制和模具技術(shù)進(jìn)步。
通過(guò)改變SMC片材加料方式和片材鋪覆位置;增加材料的流動(dòng)距離;使閉模過(guò)程中材料發(fā)生均勻位移等措施以達(dá)到減少SMC部件孔隙量。具體做法有采用PLC、 NCN控制復(fù)合材料壓機(jī)對(duì)不同部件的產(chǎn)品模壓工藝進(jìn)行對(duì)應(yīng)編程模壓控制;采用激光定位儀對(duì)材料鋪覆進(jìn)行正確定位等。另外對(duì)大型或復(fù)雜零部件采用真空輔助排氣模具,在真空條件下進(jìn)行模壓成型操作,這樣就可以顯著降低甚至消除SMC多孔性缺陷。
3. 開(kāi)發(fā)新型底漆涂料和新型涂裝工藝。
2003年BASF公司針對(duì)SMC“油漆氣泡”難題,推出DynaSeal™ 紫外固化封孔劑,這種技術(shù)使得SMC部件在噴漆烘干前,通過(guò)紫外引發(fā)聚合反應(yīng)對(duì)SMC表面進(jìn)行封孔,在接下來(lái)的噴漆油漆固化中,這層紫外固化的封孔劑層可阻止SMC基體中吸收的揮發(fā)物逸出,從而避免了氣孔的產(chǎn)生。另外一個(gè)方法就是模內(nèi)涂層(IMC)。SMC在模具內(nèi)部完全固化了之后,操作人員注入一層液體的涂層材料,然后這層涂層材料在SMC的表面固化并填充滿所有的空隙,同時(shí)提供一層類似底漆的表面,防止了油漆氣泡的產(chǎn)生。|
4. 文明生產(chǎn),文明搬運(yùn)。
SMC部件產(chǎn)生微裂紋很大程度上是從脫模到除邊的過(guò)程,以及從部件的包裝到運(yùn)輸?shù)倪^(guò)程中不文明生產(chǎn)和不文明搬運(yùn)造成的。因此加強(qiáng)文明生產(chǎn)和文明搬運(yùn)的教育至關(guān)重要,國(guó)外己普遍實(shí)行“產(chǎn)品不著地”的文明生產(chǎn)方式,在汽車復(fù)合材料行業(yè)大力推廣另件專用周轉(zhuǎn)箱(架)物流形式,減少了搬運(yùn)次數(shù),不讓另件有互相碰撞機(jī)會(huì),杜絕人為因素造成的微裂紋產(chǎn)生。
以上介紹的國(guó)外幾種新材料、新工藝、新技術(shù)著眼從根源上解決汽車復(fù)合材料在涂裝方面不盡人意的缺陷,消除限制復(fù)合材料大規(guī)模應(yīng)用的障礙,使復(fù)合材料車身面板能夠達(dá)到或超過(guò)傳統(tǒng)的鋼鐵材料的油漆的水平,從而使汽車復(fù)合材料的應(yīng)用將日益廣泛。
汽車復(fù)合材料的連接和固定
隨著汽車復(fù)合材料的應(yīng)用日益廣泛,汽車復(fù)合材料部件之間的組合裝配以及復(fù)合材料部件與鄰近金屬零部件的連接固定的問(wèn)題日益突出,汽車行業(yè)傳統(tǒng)金屬零部件之間的連接方式已不能適應(yīng)客觀需求了,在此情況下,我們有必要對(duì)汽車復(fù)合材料的連接與固定的連接方式進(jìn)行新的學(xué)習(xí)和認(rèn)識(shí),并進(jìn)行合理的選擇。根據(jù)國(guó)外成熟的經(jīng)驗(yàn),汽車復(fù)合材料連接固定的方式主要有三種方式:(1)機(jī)械緊固;(2)粘結(jié)劑粘接;(3)焊接/熔接。
機(jī)械緊固這種連接固定方法使用的是鉚釘和螺栓,是最普及也是最容易理解的一種連接方式。對(duì)汽車行業(yè)來(lái)說(shuō),機(jī)械緊固連接方式有許多不足之處,如:重量增加、應(yīng)力集中、部件之間的交迭、高公差的要求、電蝕性等。但是,從另一方面說(shuō),機(jī)械連接不需要對(duì)表面進(jìn)行處理或后續(xù)的拋光,這樣重復(fù)拆卸就很方便(如:檢查、維修和回收)。相對(duì)而言,對(duì)環(huán)境的影響也不是很敏感,如溫度的影響等。
粘結(jié)劑粘接連接固定方法相對(duì)于機(jī)械緊固連接固定方法具有以下優(yōu)點(diǎn):減輕結(jié)構(gòu)重量,外觀平整光滑,改善疲勞強(qiáng)度,適應(yīng)性強(qiáng),最適合薄壁部件的連接,粘接工藝簡(jiǎn)單,可縮短生產(chǎn)周期。,但粘結(jié)劑粘接連接固定方法也存在一些缺點(diǎn),如另部件的工作溫度范圍不高;粘接質(zhì)量易受不同因素影響,產(chǎn)品性能的分散性較大;沒(méi)有可靠的檢驗(yàn)方法;粘接面的表面處理和粘接工藝過(guò)程要求較嚴(yán);需要專用的加熱加壓處理粘接工裝等。因此,在一些重要的部件和連接位置,往往會(huì)采用粘接與某一種機(jī)械緊固連接的混合連接固定方法,既充分利用了粘接的優(yōu)點(diǎn),又確保了連接部位的足夠強(qiáng)度和可靠性。
焊接/熔接連接固定方法主要應(yīng)用于熱塑性汽車復(fù)合材料部件,焊接/熔接連接固定方法的主要優(yōu)點(diǎn)是:良好的機(jī)械性能、連接處的耐用性、加工時(shí)間短,易于在線檢測(cè)以及部件表面處理要求低等??梢杂糜跓崴苄云噺?fù)合材料的焊接/熔接連接固定方法主要有三種:(1)超聲波焊接/熔接、(2)電感應(yīng)焊接/熔接(3)電阻焊接/熔接。對(duì)汽車復(fù)合材料進(jìn)行焊接/熔接有以下不足之處:不易拆卸、需要添加導(dǎo)電性的填料(針對(duì)電感應(yīng)焊接/熔接)、需要使用金屬網(wǎng)(針對(duì)電阻焊接/熔接)、可允許的碳纖維含量很低(所有三種焊接/熔接工藝)等。
根據(jù)上述簡(jiǎn)單介紹,我們知道汽車復(fù)合材料連接固定的方式主要有三種,每一種都有各自的優(yōu)缺點(diǎn),適應(yīng)不同的應(yīng)用場(chǎng)合。但相對(duì)而言,最有發(fā)展?jié)摿Φ钠噺?fù)合材料連接工藝是采用粘結(jié)劑連接固定方法,隨著粘結(jié)劑向著功能性不斷提高、具有雙重效力(既可以粘結(jié)熱固性復(fù)合材料又可以粘結(jié)熱塑性復(fù)合材料)以及綠色環(huán)保的方向發(fā)展,汽車復(fù)合材料粘結(jié)劑連接固定方法正日益為汽車工業(yè)所重視、接受并盛行起來(lái)。限于篇幅,本節(jié)汽車復(fù)合材料的連接和固定,主要討論粘結(jié)劑粘接連接固定方法。
汽車復(fù)合材料粘結(jié)劑粘接連接固定方法的優(yōu)點(diǎn)
近年來(lái),由于高性能結(jié)構(gòu)粘結(jié)劑的出現(xiàn),使得采用粘結(jié)劑粘接的連接方式不斷得到人們的認(rèn)可。作為一種最有發(fā)展?jié)摿Φ倪B接固定工藝,它有許多突出的優(yōu)點(diǎn):
1、 可以根據(jù)具體的設(shè)計(jì)要求(如:防撞擊性能)來(lái)決定粘結(jié)劑的機(jī)械性能;
2、 粘結(jié)劑的超抗疲勞和耐腐蝕的優(yōu)點(diǎn)可以延長(zhǎng)產(chǎn)品的使用壽命;
3、 粘結(jié)劑具有很好的密封性;
4、 兩種材料或結(jié)構(gòu)粘接在一起可以實(shí)現(xiàn)比較光滑的表面,具有造型設(shè)計(jì)上的優(yōu)勢(shì);
5、 通過(guò)整個(gè)的粘接區(qū)域來(lái)分散部件所受的負(fù)荷,從而避免了局部最大壓力的集中;
6、 粘結(jié)劑填充空隙的特點(diǎn)可允許部件有一定的公差;
7、 可對(duì)粘結(jié)劑的硬度進(jìn)行調(diào)整,優(yōu)化整個(gè)產(chǎn)品的硬度
汽車復(fù)合材料常用結(jié)構(gòu)粘結(jié)劑的種類
一般來(lái)說(shuō),汽車復(fù)合材料結(jié)構(gòu)粘結(jié)劑通常使用環(huán)氧樹(shù)脂、聚氨酯樹(shù)脂和丙烯酸酯樹(shù)脂為基礎(chǔ)的三大類粘結(jié)劑,該三大類粘結(jié)劑在使用中也各具特點(diǎn),應(yīng)該準(zhǔn)對(duì)不同的材料和要求進(jìn)行不同的選擇:
環(huán)氧基粘結(jié)劑:對(duì)復(fù)合材料、熱固性塑料和金屬粘接性極好;強(qiáng)度、撓度和彈性都很高;固化過(guò)程收縮性最小。分為單、雙組份兩種。單組份環(huán)氧粘接劑要求熱固化,應(yīng)用條件要求很嚴(yán)。
聚氨酯基粘結(jié)劑:對(duì)絕大部分復(fù)合材料和塑料的粘接性極好;對(duì)金屬的粘接性較好;機(jī)械性能從剛性到撓性范圍大;持久性好;但加工過(guò)程中對(duì)潮濕敏感;固化速度的范圍較廣。
丙烯酸基粘結(jié)劑:對(duì)復(fù)合材料和熱固性塑料的粘接性極好;對(duì)金屬的粘接性好;允許被粘件進(jìn)行較差的預(yù)處理;能達(dá)到高強(qiáng)度與高韌性的最佳結(jié)合;耐化學(xué)性好,有效使用期長(zhǎng);固化速度快;但有惡臭;固化過(guò)程中收縮性較高。
表1為汽車復(fù)合材料三類結(jié)構(gòu)粘接劑的典型性能,由于結(jié)構(gòu)粘結(jié)劑的品種繁多,使用的要求又各不相同,所以應(yīng)以實(shí)際使用結(jié)構(gòu)粘結(jié)劑的性能為準(zhǔn),表中數(shù)值僅供參考。
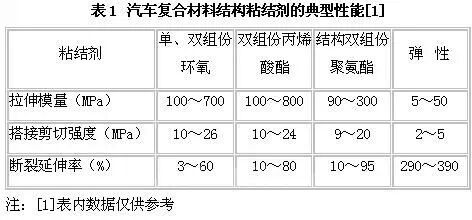
汽車復(fù)合材料粘接前的表面處理
汽車復(fù)合材料(尤其是熱塑性汽車復(fù)合材料)的表面能都相對(duì)較低,所以在使用結(jié)構(gòu)粘結(jié)劑之前,需要對(duì)汽車復(fù)合材料表面進(jìn)行適當(dāng)?shù)奶幚?,以去除表面的污垢、粉塵、油污、油脂、水分、脫模劑和增塑劑等,同時(shí),提高基材的表面能,使其高于結(jié)構(gòu)粘結(jié)劑的表面能量,從而確保結(jié)構(gòu)粘結(jié)劑能夠充分潤(rùn)濕基材表面,這對(duì)于實(shí)現(xiàn)堅(jiān)固可靠且耐久的粘接是至關(guān)重要的。下面,將介紹三種常用的表面處理方法。
1. 溶劑擦拭法
這是最簡(jiǎn)單的表面處理方式,能夠去除粘接表面的蠟質(zhì)、油污和其他小分子量的污染物。這項(xiàng)技術(shù)要求污染物可溶于溶劑,且溶劑本身不含溶解的污染物。為此,對(duì)溶劑的選擇就顯得非常重要。一般,常用的溶劑包括:丙酮、丁酮、甲基異丁基酮、二甲苯、三氯乙烯、乙醇和異丙醇等,在擦拭中應(yīng)注意使用清潔的無(wú)塵擦布或紙巾。但這種表面處理方法的缺點(diǎn)是:溶劑可能會(huì)對(duì)基材產(chǎn)生不良影響,如熱塑性復(fù)合材料可能會(huì)被溶解,顯現(xiàn)出應(yīng)力裂紋或龜裂;可能會(huì)造成交叉污染,如樣品與樣品之間的污染、重復(fù)使用或浸入到溶劑中的擦布的污染等;產(chǎn)生的蒸汽可能會(huì)危害工人的健康;不適用于大規(guī)模的生產(chǎn)要求(大規(guī)模的工業(yè)生產(chǎn)可選用蒸汽脫脂和超聲波蒸汽脫脂的方法)。
2. 打磨法
打磨可去除表面污染物,并獲得高度毛化的表面,從而增加結(jié)構(gòu)粘接劑的粘接接觸面,以產(chǎn)生“咬合效應(yīng)”。常用的打磨方法包括:采用鋼絲刷、砂紙或銼削等的手工打磨;采用砂帶、砂輪或噴丸/噴砂等的自動(dòng)打磨;以及相對(duì)較快,對(duì)操作者依賴性低且重復(fù)性和成本效益均較好的機(jī)械打磨等。
3. 火焰處理法
火焰處理是利用氣體或氣體/氧氣火焰,對(duì)表面進(jìn)行部分氧化,以產(chǎn)生極性基,從而提高聚合物的表面能。此技術(shù)所處理的基材厚度較采用電暈預(yù)處理的基材厚度大,尤其適用于不均勻的熱塑性復(fù)合材料制品。其優(yōu)點(diǎn)是:氣體與氧氣的比例、流量、暴露時(shí)間和火焰與基材的距離易于調(diào)節(jié),已被證實(shí)是適用于聚丙烯類復(fù)合材料的較有效的方法。
汽車復(fù)合材料粘接前的表面處理除了以上介紹三種常用的表面處理方法外,還有一些相對(duì)先進(jìn)和準(zhǔn)對(duì)特殊粘接要求的復(fù)雜的表面處理技術(shù),如等離子體處理 電暈放電處理 化學(xué)處理等。但無(wú)論采用那種表面處理方法,關(guān)鍵是要求有清潔的粘接表面和確保粘結(jié)劑能夠充分潤(rùn)濕基材,這是我們應(yīng)該嚴(yán)格加以關(guān)注的。
汽車復(fù)合材料粘接接頭的設(shè)計(jì)
汽車復(fù)合材料粘結(jié)劑粘接連接固定方法除了粘結(jié)劑的選擇與配制以及粘接表面處理是很關(guān)鍵的步驟外,粘接接頭的設(shè)計(jì)好壞同樣將直接影響到粘接性能和強(qiáng)度。汽車復(fù)合材料粘接接頭設(shè)計(jì)的一般原則是:保證粘接面上應(yīng)力分布均勻;將應(yīng)力減少到最小限度,使之純粹受拉力和剪切力;盡可能擴(kuò)大粘接面積等。汽車復(fù)合材料粘接接頭的結(jié)構(gòu)設(shè)計(jì)形式也是多種多樣的,根據(jù)被粘物形狀可分為平面搭接、角形搭接、T形粘接和管、棒形粘接等形式;根據(jù)材料的粘接方式又可分為對(duì)接、搭接、插接、對(duì)切雙搭接等等。從接頭形式看,一般認(rèn)為插接結(jié)構(gòu)比較理想,其次是搭接和斜搭接。但在實(shí)際應(yīng)用中,主要根據(jù)被粘接制品的結(jié)構(gòu)和需粘接的部位而具體確定。